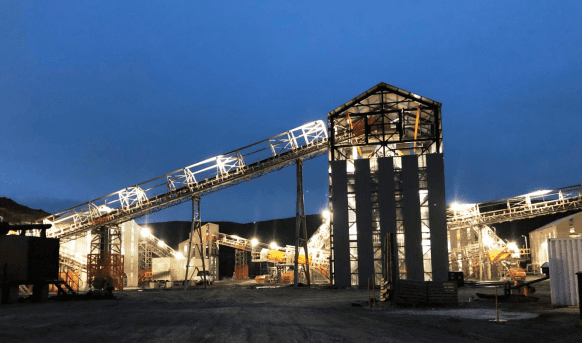
Process plants are the beating heart of many industries, from manufacturing and pharmaceuticals to food processing and energy production. Keeping these complex facilities clean is not just about aesthetics; it’s crucial for safety, efficiency, and overall plant health.
Why Cleanliness Matters in a Process Plant?
You might be thinking, “Isn’t cleaning just about making things look nice?” In a process plant, it’s far from it.
- Safety First:
- Slips, trips, and falls are common hazards in industrial settings. Clean floors free from spills, debris, and clutter significantly reduce the risk of accidents.
- Dust and grime can obscure critical safety equipment like emergency shut-off valves and fire extinguishers.
- Certain chemicals and residues can create hazardous conditions if not properly cleaned up.
- Quality Assurance:
- Contamination can compromise product quality. In food processing, even tiny particles can lead to product recalls.
- In pharmaceutical manufacturing, cleanliness is paramount to prevent cross-contamination and ensure product safety.
- Efficiency and Productivity:
- A clean plant operates more smoothly. Equipment runs more efficiently when free from obstructions.
- Regular cleaning can prevent equipment breakdowns caused by buildup of residues.
- A clean environment boosts employee morale and productivity.
- Regulatory Compliance:
- Many industries have strict regulations regarding cleanliness and hygiene. Non-compliance can result in hefty fines and even shutdowns.
Developing a Robust Cleaning Strategy
Cleaning a process plant is a multifaceted task. It requires a well-defined strategy and a dedicated team. Here’s a breakdown of key strategies:
- Risk Assessment and Prioritization:
- Identify High-Risk Areas: Pinpoint areas with the highest potential for safety hazards, contamination, or equipment damage. This might include areas with heavy equipment, chemical handling zones, and product contact surfaces.
- Prioritize Cleaning Tasks: Focus on the most critical areas first. Implement a cleaning schedule that addresses high-risk areas more frequently.
- Choosing the Right Cleaning Methods and Products:
- Select Appropriate Cleaning Agents:
- Use cleaning solutions specifically designed for different surfaces and contaminants.
- Consider eco-friendly options whenever possible.
- Ensure compatibility with equipment materials to avoid damage.
- Employ Effective Cleaning Techniques:
- Utilize high-pressure washing, steam cleaning, and other specialized methods where necessary.
- Implement dry ice blasting for delicate equipment or areas where water cannot be used.
- Training and Personnel:
- Comprehensive Training: Provide thorough training to all cleaning personnel on safety procedures, proper cleaning techniques, and the use of cleaning chemicals.
- Competent Workforce: Hire experienced cleaners with a strong understanding of industrial cleaning requirements.
- Clear Communication: Establish clear lines of communication between the cleaning crew, plant management, and equipment operators.
- Implementing a Preventative Maintenance Program:
- Regular Inspections: Conduct regular inspections of equipment and work areas to identify potential cleaning issues early on.
- Scheduled Maintenance: Implement a preventative maintenance program that includes regular cleaning and inspection of critical equipment.
- Address Issues Promptly: Address any cleaning or maintenance issues promptly to prevent them from escalating.
- Monitoring and Improvement:
- Track Cleaning Performance: Keep records of cleaning activities, including dates, times, and the areas cleaned.
- Collect Feedback: Regularly gather feedback from employees and supervisors on the effectiveness of the cleaning program.
- Continuously Improve:
- Analyze cleaning data to identify areas for improvement.
- Regularly review and update cleaning procedures as needed.
Technology in Process Plant Cleaning
Technology is playing an increasingly important role in modern process plant cleaning:
- Automated Cleaning Systems:
- Robotic systems can be used for repetitive cleaning tasks, such as floor scrubbing and high-pressure washing.
- Automated systems can improve efficiency and reduce labor costs.
- Data-Driven Cleaning:
- Utilize sensors and data analytics to monitor environmental conditions and identify areas that require more frequent cleaning.
- This data-driven approach can help optimize cleaning schedules and reduce waste.
- Virtual Reality (VR) Training:
- VR technology can be used to provide immersive training experiences for cleaning personnel.
- This can help improve safety and ensure that employees are properly trained on cleaning procedures.
The Importance of Process Plant Services Cleaning
Outsourcing Process Plant Services Cleaning can offer several benefits:
- Expertise and Experience:
- Professional cleaning companies have the expertise and experience to handle the unique challenges of cleaning industrial facilities.
- They have access to specialized equipment and cleaning agents that may not be readily available in-house.
- Cost-Effectiveness:
- Outsourcing can be cost-effective, especially for companies that don’t have the resources or expertise to manage their own cleaning operations.
- It eliminates the need to hire and train in-house cleaning staff.
- Focus on Core Business:
- Outsourcing allows companies to focus on their core business activities, rather than diverting resources to cleaning tasks.
- This can lead to increased productivity and efficiency.
- Improved Safety and Compliance:
- Professional cleaning companies are typically well-versed in safety regulations and can help ensure compliance with industry standards.
Chart: Comparing In-House vs. Outsourced Cleaning
Feature |
In-House Cleaning |
Outsourced Cleaning |
Cost |
Potential for lower initial costs |
Can be more cost-effective in the long run |
Flexibility |
Greater control over scheduling and methods |
May have limitations on scheduling and specific cleaning requirements |
Expertise |
May require ongoing training and supervision |
Access to specialized expertise and equipment |
Responsibility |
Full responsibility for safety and compliance |
Cleaning company assumes responsibility for safety and compliance |
Focus |
Can be a distraction from core business activities |
Allows companies to focus on core business activities |
Β
Conclusion
Effective Process Plant Services Cleaning is essential for safety, efficiency, and overall plant health. By implementing a robust cleaning strategy, utilizing the latest technologies, and potentially outsourcing cleaning services, companies can create a clean and safe working environment that supports optimal plant operations.
Investing in a comprehensive cleaning program is not just about keeping your plant spotless; it’s an investment in the long-term success of your business. By prioritizing cleanliness, you can reduce safety risks, improve product quality, enhance efficiency, and ensure compliance with industry regulations. A clean and well-maintained plant is a productive plant, and a productive plant is a profitable plant.
Leave a Reply