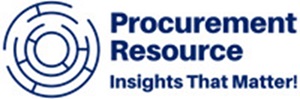
Thiophene, a five-membered aromatic compound containing one sulfur atom, plays a pivotal role in various industries. It is extensively used in the production of pharmaceuticals, agricultural chemicals, dyes, and as a building block in chemical syntheses. With the increasing demand for these end products, establishing a Thiophene manufacturing plant has become a lucrative business venture. In this comprehensive Thiophene Manufacturing Plant Project Report, we will explore the critical aspects, such as the cost model, top manufacturers, feedstocks, market drivers, manufacturing processes, and key insights.
1. Cost Model for Thiophene Manufacturing
Understanding the cost structure is crucial when setting up any chemical manufacturing plant. The production of Thiophene involves several stages, each with its cost implications, from raw material procurement to energy consumption and labor costs. The cost model for a Thiophene manufacturing plant can be divided into various categories:
Request Your Free Sample Report – https://www.procurementresource.com/reports/thiophene-manufacturing-plant-project-report/request-sample
-
Raw Materials: The cost of feedstocks such as sulfur, hydrocarbons, and other chemicals is a major contributor to the overall manufacturing cost. The price of sulfur, for example, fluctuates based on global supply and demand, which can impact the cost of Thiophene production.
-
Capital Investment: Setting up a Thiophene manufacturing plant requires substantial capital for infrastructure, machinery, and technology. The initial investment in specialized equipment like reactors, distillation columns, and filtration systems is significant.
-
Operational Costs: These include energy, labor, maintenance, and logistics. Thiophene production is energy-intensive, particularly in processes involving high temperatures or pressures.
-
Regulatory and Compliance Costs: Compliance with environmental regulations and safety standards may also add to the overall production cost. Proper waste management, emissions control, and adherence to local and international safety norms are essential.
-
Research and Development (R&D): To maintain competitive advantage and efficiency, ongoing R&D activities must be factored into the cost model. Innovations in production processes or alternate feedstock use can drive down costs over time.
To ensure profitability, businesses must accurately forecast these costs and find ways to optimize production. Procurement Resource offers a detailed cost analysis of Thiophene production, which can be beneficial for plant operators and investors.
2. Top Manufacturers in the Thiophene Industry
The Thiophene manufacturing sector is led by several prominent chemical companies that have established a global presence. These manufacturers utilize advanced technology to optimize production and meet the ever-growing demand for Thiophene and its derivatives. Some of the top players in this market include:
-
BASF SE: Known for its extensive portfolio of chemicals, BASF is a key producer of Thiophene-based compounds, serving industries like pharmaceuticals, agrochemicals, and electronics.
-
SABIC: Another industry giant, SABIC manufactures Thiophene derivatives that find applications in a wide range of products, from plastics to industrial chemicals.
-
Evonik Industries: This German company is a leader in specialty chemicals and has a strong foothold in Thiophene production, especially in the pharmaceutical sector.
-
Afton Chemical Corporation: Specializing in fuel additives, Afton Chemical also manufactures Thiophene and its derivatives for various industrial applications.
-
LANXESS AG: A leading global chemical manufacturer, LANXESS produces Thiophene for applications in the automotive, electronics, and pharmaceutical industries.
3. Outline of a Thiophene Manufacturing Plant
The design and construction of a Thiophene manufacturing plant require careful planning to ensure the efficient production of high-quality Thiophene while minimizing costs. The typical plant structure includes:
-
Feedstock Handling Area: This is where the raw materials are stored, prepared, and transferred to the production process.
-
Reactor System: The core of the manufacturing process, where sulfur and hydrocarbons are chemically reacted to form Thiophene. This system is highly energy-intensive, requiring careful temperature and pressure control.
-
Separation and Purification Units: After synthesis, Thiophene needs to be separated from byproducts and purified. Distillation columns, filtration systems, and other separation techniques are used to ensure high-quality output.
-
Packaging and Distribution Section: Once Thiophene is produced and purified, it is packaged and prepared for distribution to customers worldwide.
-
Waste Treatment Facilities: Thiophene production generates waste, including sulfuric compounds and organic solvents. Treatment plants are necessary to handle these byproducts and comply with environmental regulations.
Read Full Report With Table Of Contents: https://www.procurementresource.com/reports/thiophene-manufacturing-plant-project-report/toc
4. Feedstocks for Thiophene Production
The primary feedstocks for Thiophene production are sulfur and hydrocarbons, specifically those containing five carbon atoms, like butanes and pentanes. These feedstocks are readily available in the chemical industry, and their prices are influenced by global market trends. Other potential feedstocks include:
-
Petroleum Derivatives: Petroleum is rich in hydrocarbons, which can be processed to produce Thiophene.
-
Coal: Coal can be processed through gasification to generate the necessary sulfur-rich feedstocks.
The availability of these feedstocks significantly impacts the cost structure of a Thiophene manufacturing plant. Market fluctuations in the price of crude oil, natural gas, and sulfur can drive up costs, necessitating proactive supply chain management and strategic sourcing.
5. Market Drivers for Thiophene Production
The demand for Thiophene is driven by several key factors, which include:
-
Pharmaceutical Industry: Thiophene is a vital building block for the synthesis of several pharmaceutical compounds, including those used in the treatment of cardiovascular diseases, diabetes, and cancer. With the growing global population and increasing healthcare needs, the pharmaceutical sector remains a major driver of Thiophene demand.
-
Agricultural Chemicals: Thiophene derivatives are used to create fungicides and insecticides, critical for ensuring crop protection in agriculture. The rising demand for food security and sustainable farming practices will continue to spur growth in this sector.
-
Petrochemical Industry: Thiophene is also used in the production of synthetic polymers and resins, which are essential in various industries, including packaging, automotive, and construction.
-
Electronics: As the electronics industry expands, Thiophene derivatives are increasingly used in the production of electronic components, such as organic semiconductors, photovoltaic cells, and light-emitting diodes (LEDs).
-
Environmental Regulations: Stringent environmental regulations are encouraging the development of more efficient and sustainable Thiophene production methods, further promoting growth in the sector.
6. Manufacturing Process of Thiophene
The synthesis of Thiophene involves several chemical reactions, with the most common methods being:
-
The Diels-Alder Reaction: This process involves reacting a diene (like butadiene) with a dienophile (such as sulfur) to form Thiophene. This method is favored for its simplicity and efficiency.
-
The Cyclization of 1,3-Dienes with Sulfur: Another popular method is the cyclization of unsaturated hydrocarbons with sulfur, which leads to the formation of Thiophene. This process is used in industrial-scale production.
-
Hydrothermal Synthesis: In this method, sulfur and hydrocarbons are subjected to high-pressure, high-temperature conditions in the presence of water to produce Thiophene. While energy-intensive, this method is gaining popularity for its high yield.
7. Key Insights on Thiophene Manufacturing
-
Technological Innovations: Continuous advancements in Thiophene production technologies are making the process more efficient, reducing waste and energy consumption. Catalysis plays a significant role in optimizing reaction conditions, reducing costs, and improving yields.
-
Global Market Trends: The Thiophene market is witnessing steady growth due to its increasing demand across industries. The rise of emerging markets, particularly in Asia-Pacific, is further driving market expansion.
-
Sustainability: Sustainable manufacturing practices, such as green chemistry and waste minimization, are becoming increasingly important in the Thiophene industry. Plant operators are adopting eco-friendly technologies to reduce environmental impact.
-
Profitability: Despite challenges such as fluctuating raw material costs and strict regulations, Thiophene manufacturing remains a profitable venture, especially with a well-designed cost model and strategic market positioning.
The Thiophene Manufacturing Plant Project Report outlines the essential components of setting up a Thiophene manufacturing plant. By understanding the cost structure, key manufacturers, and market dynamics, investors and manufacturers can make informed decisions. The continuous evolution of the manufacturing process, coupled with innovations in feedstock sourcing and sustainability practices, ensures that Thiophene will remain a crucial compound in various industrial sectors for years to come. For detailed insights into this growing market, Procurement Resource provides in-depth data and analysis on Thiophene production costs and trends, aiding businesses in making strategic decisions.
Contact Us:
Company Name: Procurement Resource
Contact Person: Endru Smith
Email: sales@procurementresource.com
Toll-Free Number: USA & Canada - Phone no: +1 307 363 1045 | UK - Phone no: +44 7537171117 | Asia-Pacific (APAC) - Phone no: +91 1203185500
Address: 30 North Gould Street, Sheridan, WY 82801, USA
Leave a Reply