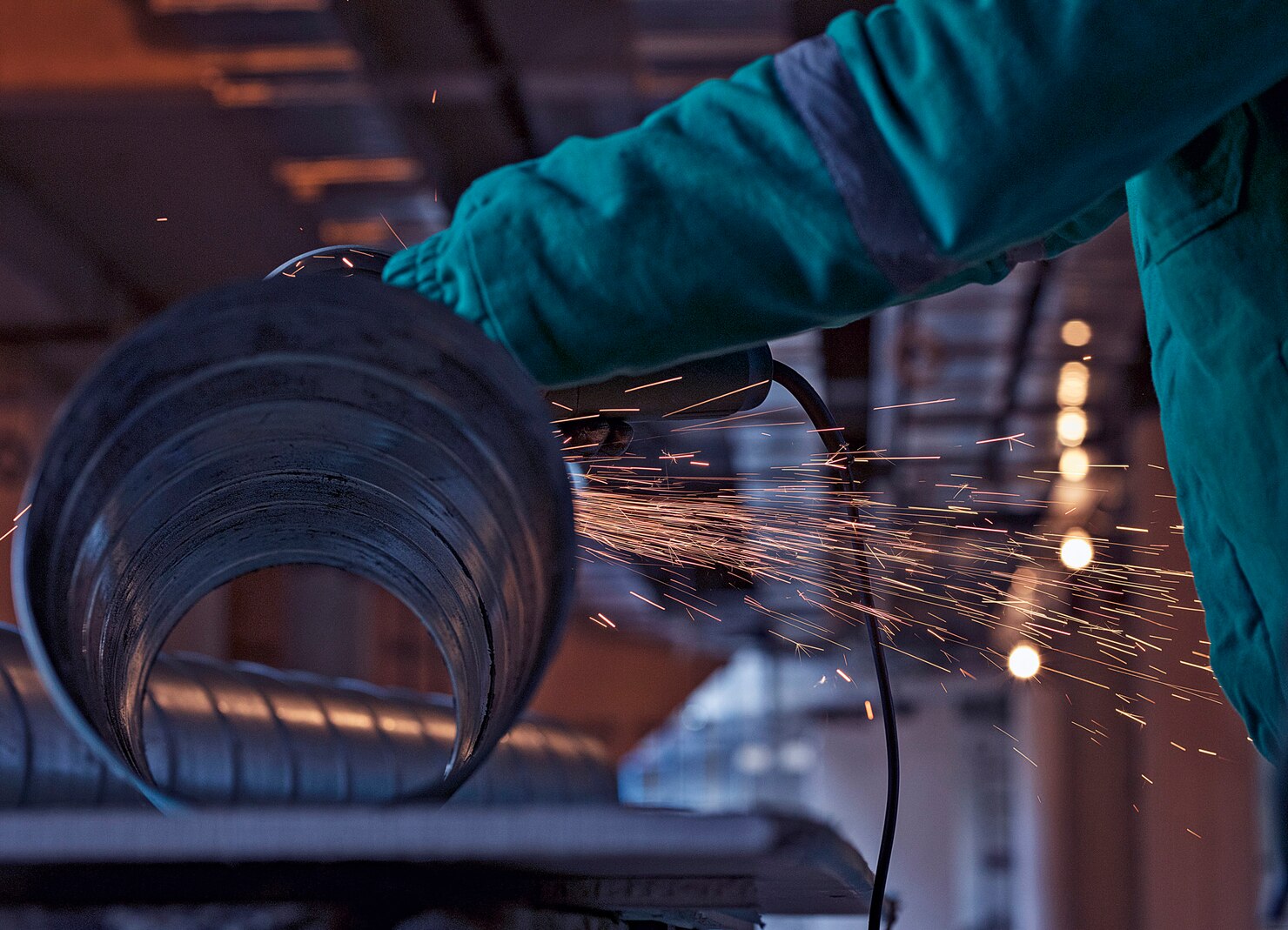
The future of metal fabrication is poised to witness transformative changes driven by technological advancements, shifting market demands, and a greater focus on sustainability. As industries such as automotive, aerospace, and construction continue to evolve, so too must the metal fabrication processes that support them. The increasing reliance on automation, the integration of artificial intelligence (AI), and the adoption of greener practices are reshaping how metal fabrication is carried out. In this article, weβll explore these trends, offering key insights into what the future holds for the metal fabrication industry.
The Role of Automation in Metal Fabrication
One of the most significant changes the future of metal fabrication is expected to see is the widespread adoption of automation. Automation in metal fabrication involves the use of robotic systems, CNC machines, and other advanced technologies to perform tasks such as cutting, welding, and assembly. These systems improve production speed, reduce human error, and enhance precision. In the future, we can expect an even greater reliance on automation to meet the growing demands for customized products and faster production cycles.
Automated systems in metal fabrication also offer improvements in worker safety by reducing their exposure to hazardous tasks. As robots and machines handle the most dangerous aspects of the job, human workers will be able to focus on more complex and less physically demanding tasks. This shift is expected to create new opportunities for skilled workers who can operate and maintain these advanced systems, marking a crucial shift in the workforce within the industry.
Advancements in Digitalization and AI
The integration of digital tools and artificial intelligence (AI) is another key development that will define the future of metal fabrication. Digital technologies such as 3D printing, computer-aided design (CAD), and simulation software are already enhancing the design and prototyping stages of metal fabrication. Moving forward, AI and machine learning will become even more integrated into the production process, enabling manufacturers to make smarter, data-driven decisions that improve efficiency and product quality.
AI can also be used to predict machine maintenance needs, thus reducing downtime and preventing costly breakdowns. Predictive analytics, powered by AI, will allow metal fabricators to optimize their operations, forecast demand, and adjust production schedules accordingly. These technologies not only make the fabrication process more efficient but also help companies stay competitive in a market where innovation is key to success.
Sustainability and Green Initiatives
As industries across the globe increasingly prioritize sustainability, the future of metal fabrication will undoubtedly be influenced by the demand for greener practices. Metal fabrication processes are energy-intensive, and traditionally, they have contributed to environmental challenges such as waste and emissions. However, in response to growing environmental concerns, the industry is beginning to adopt more sustainable practices, including the use of recycled materials, energy-efficient machines, and cleaner production methods.
In addition to reducing the carbon footprint of metal fabrication, the use of environmentally friendly materials and processes is also driven by consumer preferences for sustainable products. For example, the automotive and construction industries are looking to reduce their environmental impact by using lighter, stronger, and more sustainable metals. In the future, the metal fabrication industry will likely see increased demand for innovations such as bio-based metals and energy-efficient fabrication techniques that minimize waste and environmental harm.
The Impact of 3D Printing on Metal Fabrication
Additive manufacturing, or 3D printing, is another technology that is rapidly shaping the future of metal fabrication. In recent years, 3D printing has gained traction in industries like aerospace, automotive, and healthcare for its ability to create complex and customized metal parts without the need for traditional machining. This technology allows for rapid prototyping, which significantly reduces lead times and production costs while enabling the creation of parts that were previously difficult or impossible to manufacture.
As 3D printing technologies continue to evolve, we can expect even greater capabilities in metal fabrication. For instance, future 3D printers may be able to print larger and more intricate metal components with greater precision and speed. Furthermore, the adoption of 3D printing in metal fabrication will likely lead to more localized production, reducing supply chain complexities and enabling companies to respond more quickly to market demands.
The Evolution of Workforce Skills and Training
With all these technological advancements, the future of metal fabrication will require a shift in workforce skills and training. As automation, AI, and 3D printing become more prevalent, the demand for traditional manual labor may decrease, while the need for highly skilled workers who can operate and troubleshoot advanced machinery will grow. Companies will need to invest in training programs to ensure that their employees have the necessary expertise to manage cutting-edge technologies and adapt to evolving industry standards.
In the future, itβs likely that vocational schools and universities will offer specialized training programs focused on advanced manufacturing techniques, robotics, and digital technologies. By preparing workers for the changing landscape of metal fabrication, the industry can ensure a smooth transition toward these innovative processes while maintaining a competitive edge in the global market.
Conclusion
The future of metal fabrication is bright and full of potential. Driven by technological innovations like automation, AI, 3D printing, and sustainable practices, the industry is evolving at a rapid pace. These advancements promise to increase efficiency, improve product quality, and reduce the environmental impact of metal fabrication. However, the success of these developments will largely depend on the industryβs ability to adapt to new technologies and ensure that its workforce is equipped with the skills needed for the next generation of manufacturing. As we look ahead, it is clear that metal fabrication will continue to play a crucial role in shaping the industries of tomorrow.
Leave a Reply