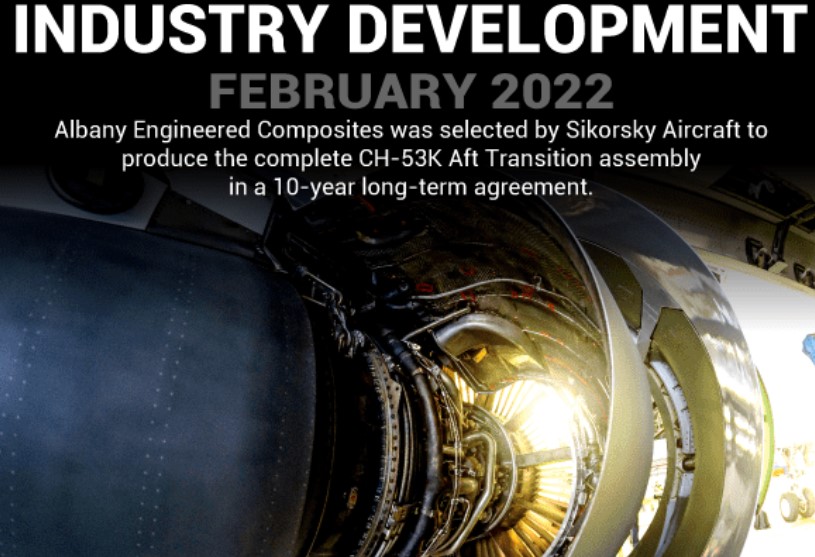
The global aero composite materials market size was worth $2.53 billion in 2021. It is expected to grow steadily, reaching $2.87 billion in 2022 and climbing to $5.17 billion by 2029, with an average annual growth rate of 8.76% during this period. In 2021, North America led the market, holding a 38.74% share.
Informational Source:
https://www.fortunebusinessinsights.com/aero-engine-composite-material-market-105538
The aerospace industry has been undergoing a transformative phase, with composite materials playing a pivotal role in advancing performance, fuel efficiency, and sustainability. Aero composite materials, primarily used in manufacturing aircraft structures and components, have become indispensable due to their superior strength-to-weight ratio, corrosion resistance, and design flexibility. This article explores the latest developments, market trends, and future prospects of aero composite materials, emphasizing their applications, innovations, and market dynamics.
Key Companies Covered In Aero Engine Composite Material Market are:
- Rolls Royce Holdings Plc (U.K.)
- GE Aviation (U.S.)
- Hexcel Corporation (U.S.)
- Meggitt Plc (U.K.)
- Albany International (U.S.)
- Nexcelle LLC (U.S.)
- Solvay (Belgium)
- DuPont de Nemours, Inc. (U.S.)
- Safran SA (France)
- FACC AG (Austria)
Overview of Aero Composite Materials
Aero composite materials are engineered substances composed of two or more distinct materials, such as fibers (reinforcement) and matrices (resin or metal). These materials are designed to combine the best properties of their constituents, making them ideal for the demanding conditions of aerospace applications. Commonly used composites include:
-
Carbon Fiber Reinforced Polymers (CFRP): Known for their lightweight and high strength, CFRPs are extensively used in aircraft fuselages, wings, and engine components.
-
Glass Fiber Reinforced Polymers (GFRP): Although less strong than CFRPs, GFRPs are cost-effective and widely used in secondary structures.
-
Ceramic Matrix Composites (CMC): These are primarily used in high-temperature environments, such as jet engine components.
-
Aramid Fiber Composites: Used in areas requiring high impact resistance, such as protective structures.
Key Market Drivers
-
Fuel Efficiency and Weight Reduction: Airlines and aircraft manufacturers prioritize fuel efficiency, leading to increased adoption of lightweight materials. Composite materials significantly reduce aircraft weight compared to traditional metals like aluminum and titanium.
-
Increased Aircraft Production: The rising demand for commercial and military aircraft globally has boosted the adoption of composite materials in new-generation aircraft, such as the Boeing 787 and Airbus A350, which use over 50% composites by weight.
-
Stringent Environmental Regulations: Governments and international organizations are enforcing stricter emissions standards. Composite materials help reduce fuel consumption and greenhouse gas emissions, aligning with sustainability goals.
-
Technological Advancements: Innovations in composite manufacturing processes, such as automated fiber placement (AFP), resin transfer molding (RTM), and 3D printing, have enhanced production efficiency and material properties.
Applications of Aero Composite Materials
-
Aircraft Structures:
-
Fuselage and Wings: Composites enable lightweight and aerodynamically efficient designs, improving fuel efficiency.
-
Control Surfaces: Used in ailerons, flaps, and elevators for precise and responsive control.
-
-
Engine Components:
-
High-performance composites like CMCs are employed in fan blades, casings, and turbine components to withstand extreme temperatures and reduce weight.
-
-
Interior Components:
-
Cabin structures, seats, and overhead compartments benefit from composites for enhanced durability and weight savings.
-
-
Rotorcraft and UAVs:
-
Helicopter blades and unmanned aerial vehicle (UAV) structures rely heavily on composite materials for optimal performance and endurance.Recent Innovations and Developments
-
-
Next-Generation Composites:
-
Researchers are exploring hybrid composites combining multiple fibers (e.g., carbon and glass) to achieve tailored properties.
-
Self-healing composites are under development, capable of repairing damage autonomously, thus enhancing durability and reducing maintenance costs.
-
-
Sustainable Composites:
-
Bio-based resins and recyclable composites are gaining traction, aligning with the industry’s push for greener materials.
-
-
Advanced Manufacturing Techniques:
-
Automated fiber placement and additive manufacturing are enabling precise and scalable production of complex composite parts.
-
High-pressure resin transfer molding (HP-RTM) is reducing cycle times, making composites more cost-competitive.
-
-
Smart Composites:
-
Integration of sensors and actuators into composites allows real-time monitoring of structural health, enhancing safety and reliability.Challenges in the Aero Composite Materials Market
-
-
High Costs:
-
Composite materials and manufacturing processes are expensive compared to traditional materials, posing a challenge for widespread adoption.
-
-
Recycling and Disposal:
-
The industry faces challenges in recycling thermoset composites, which are commonly used in aerospace applications.
-
-
Complex Manufacturing Processes:
-
Advanced manufacturing methods require significant investment in infrastructure, skilled labor, and quality control.
-
-
Regulatory Compliance:
-
Aerospace composites must meet stringent safety and performance standards, which can prolong certification processes.Market Trends and Dynamics
-
-
Market Size and Growth:
-
The global aero composite materials market was valued at USD 2.53 billion in 2021 and is projected to grow at a compound annual growth rate (CAGR) of 8.76%, reaching USD 5.17 billion by 2029.
-
-
Regional Insights:
-
North America: Dominates the market with significant aerospace manufacturing hubs and leading composite material suppliers.
-
Europe: Home to major aircraft manufacturers like Airbus, Europe is a key market for aero composites.
-
Asia-Pacific: Rapidly emerging as a growth center due to increasing aircraft production and rising investments in aerospace infrastructure.
-
-
Competitive Landscape:
-
Leading players in the market include Hexcel Corporation, Solvay, Toray Industries, and SGL Carbon, among others. These companies are investing in R&D to develop advanced composite solutions.Future Outlook
-
The future of aero composite materials looks promising, driven by advancements in material science, manufacturing technologies, and the push for sustainability. Key trends to watch include:
-
Increased Use in Space Applications:
-
Composite materials are finding applications in satellite structures, rocket casings, and space exploration vehicles.
-
-
Collaborative R&D Efforts:
-
Partnerships between aerospace companies, research institutions, and material manufacturers are accelerating innovation.
-
-
Focus on Lifecycle Management:
-
Development of composites with better recyclability and longer lifecycles to reduce environmental impact.
-
Leave a Reply