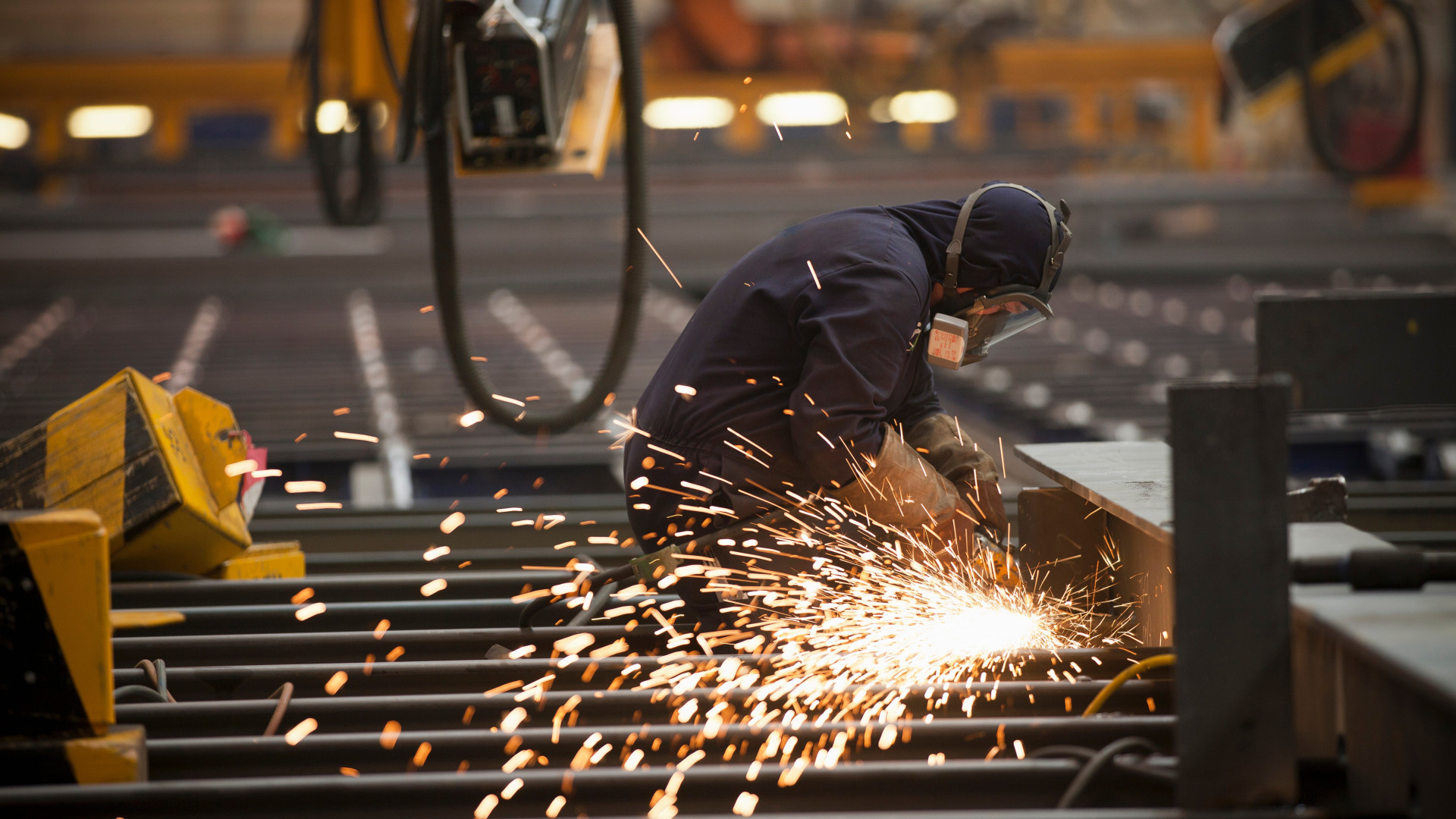
Steel structure fabrication provides the foundation for creating grand structures such as tall buildings, large warehouses, or strong bridges. Workers process steel parts by cutting them, shaping them, and placing them together to create more real, solid structures through designs. Steel is pretty strong and flexible, but it lasts long, making even small mistakes and big headaches. These errors can make the building unsafe, cost extra money for projects, and slow a project down. If you wish to work on construction or are a fan of learning about it, it will help you build better and smarter with these common mistakes, their effects, and how to avoid them. Using the proper skills and keen attention to detail, these steel structures will stand tall for decades and ensure safety and success in every project.
1. Inaccurate Measurements
Accurate measurements are essential to ensure steel components fit together seamlessly. Even minor errors during measurement or cutting can cause significant problems down the line. When parts donโt align or fit as intended, the entire structure can become unstable.
Common Causes of Inaccurate Measurements:
- Relying on outdated or manual measuring tools.
- Human error during calculations or measurements.
- Failure to verify dimensions against the design blueprint.
- Rushing through the measurement process to save time.
Consequences of Inaccurate Measurements:
- Misalignment Issues: Poorly measured components may not align properly, which weakens the structure and delays assembly.
- Material Waste: Incorrect cuts mean materials need to be discarded or recut, increasing costs.
- Delays: Reworking steel components adds significant time to project timelines.
Example:
Suppose steel beams for a warehouse are cut 1 centimetre too long. When the beams are assembled, they fail to connect correctly, causing misalignment and forcing the team to halt construction to correct the issue.
How to Avoid Inaccurate Measurements:
- Use advanced tools like laser cutting machines and digital callipers for precision.
- Verify measurements multiple times before cutting steel.
- Cross-check dimensions against detailed design drawings or CAD (Computer-Aided Design) models.
- Train workers to measure carefully and prioritize precision over speed.
2. Using Low-Quality Materials
Steel structures depend heavily on the quality of materials used during fabrication. Some fabricators, in an effort to cut costs, may opt for substandard steel. However, poor-quality materials result in structures that are weak, unsafe, and prone to damage.
Common Reasons for Using Low-Quality Materials:
- Pressure to reduce costs and meet tight budgets.
- Lack of supplier research and reliance on unverified vendors.
- Absence of proper material quality control processes.
Consequences of Low-Quality Materials:
- Weakened Structures: Inferior steel may not support the intended load, leading to cracks, bending, or collapse.
- Faster Corrosion: Poor-quality steel corrodes more quickly, shortening the lifespan of the structure.
- Safety Risks: Structures built with substandard materials may fail under stress, posing serious safety hazards.
Example:
A pedestrian bridge built using low-grade steel might appear sturdy initially but could develop cracks after a year, creating a safety risk and requiring costly repairs.
How to Avoid Material Quality Issues:
- Source steel only from certified, reputable suppliers.
- Test steel for quality, including strength, durability, and resistance to corrosion.
- Ensure the steel meets industry standards and project requirements.
- Avoid compromising material quality to save moneyโthis short-term โsolutionโ often leads to long-term problems.
3. Improper Welding Techniques
Welding is one of the most critical processes in steel structure fabrication. It joins steel components together to create strong, stable connections. However, improper welding can compromise the integrity of the entire structure.
Common Welding Mistakes:
Incorrect Technique: Choosing the wrong welding method for certain types of steel can ruin connections.
Uneven Heat Application: Applying too much or too little heat can bend steel out of shape and weaken its joints.
Weakened or Irregular Welds: Poor welds can crack, break, or split and create dangerous weak points.
Consequences of Improper Welding:
Structural Weakness: Cracked welds weaken bonds and make the structure unsteady and unsafe.
Increased Maintenance: Poor welds require constant repairs, which is a time and resource waste.
Safety Issues: ย The consequences of improper welding are parts failure which causes accidents and injuries.
Example:
The steel columns of a tall building hold beams together through strong welds. If welders leave gaps or uneven welds, the columns may crack under pressure, putting the entire building at risk of falling apart.
How to Avoid Welding Mistakes:
- Train welders to use the appropriate techniques for different types of steel.
- Ensure welders are certified and experienced in handling structural projects.
- Use welding equipment that allows precise heat control to prevent distortion.
- Inspect welds frequently for cracks, gaps, and defects to identify issues early.
4. Neglecting Surface Preparation and Finishing
Preparing the surface of steel is critical to shield structures from rust, corrosion, and harsh weather. However, some fabricators skip this important step or rush through it, which weakens the steel and shortens its life.
Why Surface Preparation Matters:
- Protection Against Corrosion: Proper finishes block moisture, chemicals, and pollutants from eating away at the steel.
- Improved Adhesion: Cleaning and preparing the surface helps paints and coatings stick firmly and last longer.
- Longer Lifespan: Well-prepared and finished steel stays strong for years and needs fewer repairs.
Common Surface Preparation Mistakes:
- Skipping cleaning steps like grinding, sandblasting, or removing rust.
- Apply paint or coatings on surfaces covered with dirt, grease, or oil.
- Choosing poor-quality or unsuitable protective coatings that fail quickly.
Example:
Steel structures in coastal areas face constant attacks from salty air. Moreover, if workers leave the steel uncleaned or apply weak coatings, rust will spread quickly. Over time, the steel grows weak, requiring costly repairs to fix the damage.
How to Avoid Surface Preparation Errors:
- Clean steel surfaces completely using sandblasting, grinding, or chemical treatments to remove rust and dirt.
- Eliminate contaminants like grease, oil, and dust before applying coatings.
- Use strong, weather-resistant coatings such as high-quality paint, epoxy, or galvanization to protect the steel.
- Match the protective finish to the environmentโchoose coatings that withstand humidity, salt, or chemicals.
5. Poor Planning and Communication
Steel structure fabrication requires a clear and detailed plan, as well as seamless communication between stakeholders. Planning or communication can result in errors, delays, and added expenses.
Common Causes of Poor Planning:
- Lack of coordination between design, fabrication, and construction teams.
- Frequent design changes without proper documentation.
- Unclear or incomplete project specifications.
Consequences of Poor Planning and Communication:
- Errors in Fabrication: Misunderstood blueprints lead to incorrectly fabricated components.
- Project Delays: Confusion and rework slow down progress.
- Increased Costs: Fixing mistakes caused by poor communication is expensive.
Example:
If a designer modifies the specifications for steel trusses without informing the fabrication team, the resulting trusses might not fit during assembly, causing delays.
How to Avoid Poor Planning:
- Develop a clear project timeline and share it with all teams.
- Use project management tools to track progress and address issues quickly.
- Maintain regular communication between design, fabrication, and construction teams.
- Document all changes and ensure everyone is informed about updates.
Why Avoiding These Mistakes Is Critical
By avoiding the five most common mistakes in steel structure fabrication, one can therefore guarantee that projects will be finished on time, under budget, and of high quality. Indeed, precision measurements, superior materials, appropriate welding, proper surface preparation, and planning all play a significant role in developing stronger, safer, and more resilient structures.
Helpful Tips to Improve Steel Fabrication Quality
To make the steel structure fabrication process stronger and more reliable, follow these helpful tips:
- Invest in Advanced Tools: Use tools like laser cutters, automated machines, and digital software to shape steel with perfect accuracy.
- Focus on Quality Control: Check the materials, welds, and finishes carefully at every step to catch and fix mistakes early.
- Train the Workforce: Teach workers new skills regularly to sharpen their abilities and maintain top-quality work.
- Prioritize Safety: Follow safety protocols to protect workers and ensure long-term structural integrity.
- Communicate Clearly: Foster collaboration between design teams, fabricators, and contractors.
- Use Certified Materials: Always test and verify the steelโs quality before use.
Conclusion
Errors in steel structure fabrications may result in several costly delays, structural collapses, and even safety risks. Understanding and avoiding mistakes such as inadequate measurements, low-quality material, poor welding, inferior surface preparation, and poorly planned works will ensure better quality. The bottom line is precision, attention to detail, and clear communication to ensure the best results; hence, strong, safe, and long-lasting constructions that are up to standard in the industry.
Leave a Reply