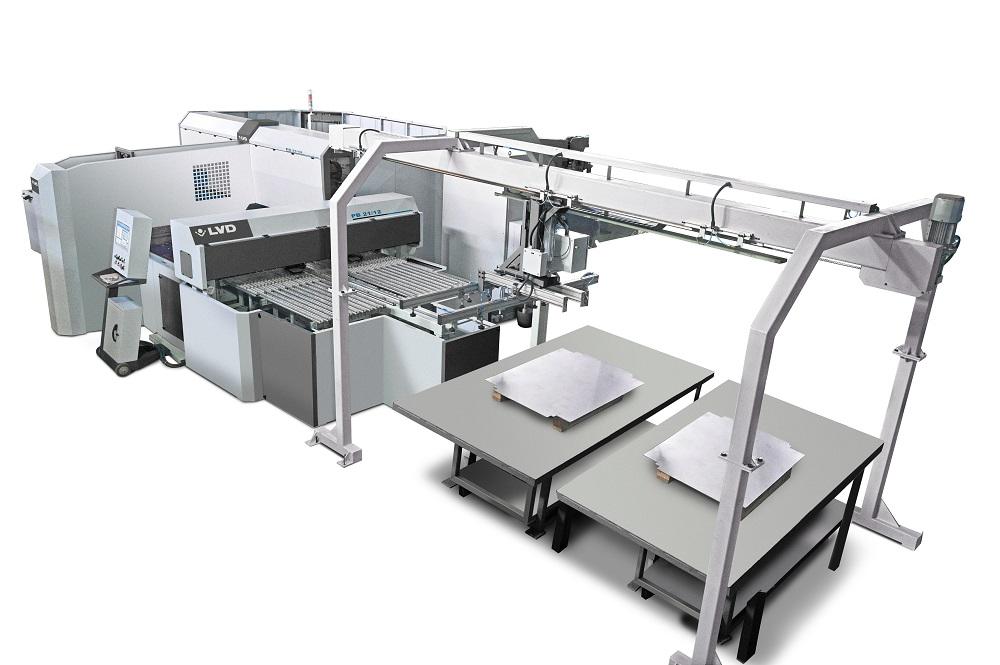
In the world of metal fabrication, precision and efficiency are paramount. Whether you’re creating intricate sheet metal components or large-scale industrial parts, the choice of equipment can make all the difference. Two of the most commonly used tools in the bending process are panel benders and press brakes. But how do you decide which is the right tool for your needs? Letโs break it down.
Understanding the Basics
Panel Benders Panel benders are automated machines designed for high-speed, high-precision bending of sheet metal. They are particularly effective for repetitive tasks and are often used in industries like automotive, aerospace, and electronics manufacturing. A panel benderโs automated nature allows for consistent results and reduced labor requirements.
Press Brakes Press brakes are versatile machines that use a punch and die to shape metal sheets. They offer greater flexibility in terms of design and customization, making them ideal for projects that require unique or complex bends. Operators play a significant role in ensuring accuracy, making press brakes more dependent on skilled labor.
Key Differences Between Panel Benders and Press Brakes
-
Automation and Efficiency
-
Panel Benders: These machines excel in automation. With programmable settings, they can handle large production volumes with minimal manual intervention. Their ability to execute multiple bending operations in one cycle significantly reduces production time and enhances efficiency.
-
Press Brakes: While many press brakes now come with CNC technology, they often require more hands-on operation, especially for custom projects. This makes them slower in high-volume production compared to panel benders.
-
-
Precision
-
Panel Benders: Ideal for high-precision tasks, they deliver consistent results with tight tolerances, making them perfect for mass production. The automated nature of panel benders ensures uniformity across all parts, eliminating human error.
-
Press Brakes: Precision depends heavily on the operatorโs skill and the machineโs calibration. They can achieve high accuracy but may require more effort for consistency, particularly when working on complex projects.
-
-
Flexibility
-
Panel Benders: Best suited for standardized bends and repetitive tasks. Their limitations lie in handling very thick or unusually shaped metal sheets. However, they excel at producing components like enclosures, panels, and chassis with consistent quality.
-
Press Brakes: Highly versatile, they can accommodate a wide range of materials, thicknesses, and bend designs. This makes them ideal for projects that require unique geometries or irregular bends.
-
-
Cost and Investment
-
Panel Benders: Higher upfront costs due to automation and advanced technology, but they offer long-term savings in labor and production time. The return on investment is particularly high for manufacturers with large-scale production needs.
-
Press Brakes: Generally more affordable upfront, but they may incur higher operational costs due to labor and longer production times. They are often the go-to choice for small to medium-sized operations.
-
Applications: When to Use Each Tool
Choose a Panel Bender if:
-
You need to produce large quantities of identical parts.
-
Precision and consistency are critical to your operation.
-
Your business prioritizes automation and efficiency over flexibility.
-
You work with materials of uniform thickness and standard shapes.
Choose a Press Brake if:
-
Your projects require unique or complex bends.
-
You work with a variety of materials and thicknesses.
-
Flexibility and customization are important for your operation.
-
Youโre handling low to medium production volumes.
Case Studies: Real-World Applications
Panel Benders in Action A large-scale automotive manufacturer needed to produce thousands of identical metal panels for car doors. They opted for a CNC panel bender to automate the process, achieving consistent precision and significantly reducing production time. The automation also allowed them to allocate their workforce to other critical tasks, further improving operational efficiency.
Press Brakes in Action A custom metal fabrication shop specializing in architectural components chose a press brake to handle a variety of projects. From creating intricate decorative panels to producing one-off prototypes, the press brakeโs versatility allowed them to meet diverse client needs without investing in multiple machines.
Advancements in Technology
Both panel benders and press brakes have seen significant advancements in recent years. Modern CNC panel benders come equipped with features like automatic tool changes, advanced sensors, and software integration, making them smarter and more efficient. Similarly, CNC press brakes now offer capabilities like 3D simulation, touch-screen interfaces, and AI-driven error detection, bridging the gap between automation and manual control.
Additionally, hybrid machines that combine features of panel benders and press brakes are emerging, offering manufacturers the best of both worlds. These machines are particularly useful for operations that require both high-volume production and occasional customization.
Pros and Cons at a Glance
Feature | Panel Bender | Press Brake |
---|---|---|
Automation | High (minimal manual intervention) | Moderate (requires skilled operators) |
Precision | Excellent (consistent results) | Good (depends on operator skill) |
Flexibility | Limited (standardized tasks) | High (versatile applications) |
Cost | High upfront, long-term savings | Lower upfront, higher operational |
Production Volume | Best for high-volume production | Suitable for low to medium volumes |
Making the Decision
Choosing between a panel bender and a press brake is not a one-size-fits-all decision. It depends on factors like production volume, project complexity, material types, and budget. Here are some questions to help guide your choice:
-
What is the primary type of work your business handles? If youโre focused on high-volume, repetitive production, a panel bender is likely your best option.
-
Do you need flexibility to create custom or unique designs? If so, a press brake offers the versatility you need.
-
How important is automation to your operation? For businesses looking to minimize manual labor and maximize efficiency, panel benders are a clear winner.
-
What is your budget for equipment and operational costs? Consider both the upfront investment and long-term savings when evaluating your options.
The Future of Metal Bending
As technology continues to evolve, the gap between panel benders and press brakes is narrowing. Manufacturers are increasingly integrating features like AI, IoT connectivity, and real-time monitoring into these machines, enhancing their capabilities and making them more user-friendly. The future of metal bending lies in hybrid solutions that combine automation with flexibility, allowing businesses to adapt to changing demands with ease.
Conclusion
Both panel benders and press brakes play essential roles in the metal fabrication industry. By understanding their unique strengths and limitations, you can choose the right tool for your needs. Whether you prioritize precision, flexibility, or cost-efficiency, selecting the right equipment will ensure your operation runs smoothly and delivers high-quality results.
Investing in the right bending technology is not just about meeting todayโs demands; itโs about preparing for the future. With advancements in automation and smart manufacturing, the choice you make now will set the foundation for your businessโs long-term success.
Leave a Reply