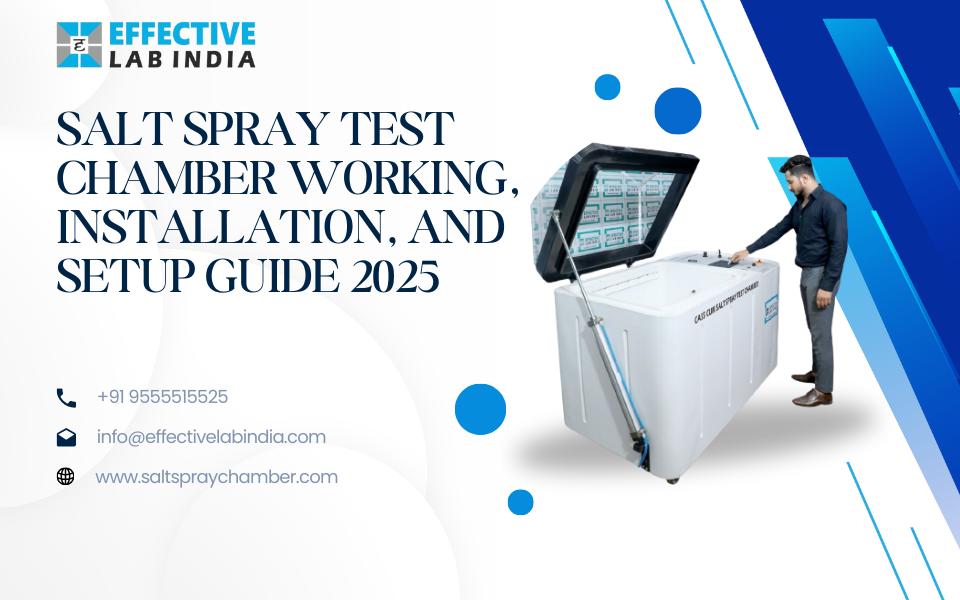
Corrosion is a silent degradation agent capable of long-term damage and disruption of function. This is why salt spray testing is so important for the automotive, aerospace, and marine industries. In this guide, we’ll explore the salt spray chamber—its operating procedure, installation, configuration, and important role in quality assurance.
What is a Salt Spray Test Chamber?
The salt spray test chamber is a controlled environment designed to evaluate the corrosion resistance of materials and coatings. Simulating harsh environmental conditions helps manufacturers predict the long-term performance of their products.
or
The salt spray chamber is an important test device used in electroplating to evaluate the corrosion resistance of coated materials. It helps in determining the durability and efficiency of the electrical installation by subjecting it to harsh environmental conditions such as saline air and humidity. These tests are essential to ensure product longevity in the automotive, marine, and aerospace industries, where protection against corrosion and corrosion is important.
Industries that Use Salt Spray Testing
The salt spray test chamber is essential in any industry where corrosion resistance is crucial, from maritime equipment to automobile parts.
Why Salt Spray Testing is Crucial
Knowing How to Prevent Corrosion
Corrosion can cause material failure, monetary losses, and safety risks. Testing with salt spray guarantees that materials can withstand practical difficulties.
Advantages for Researchers and Manufacturers
This test ensures customer pleasure and trust by improving product quality and reducing recall risk.
Components of a Salt Spray Test Chamber
Typical salt spray test chambers include:
- Testing Chamber: The primary area where specimens are placed.
- Salt Solution Reservoir: Stores the salt solution for spraying.
- Nozzle System: Distributes the solution evenly among the samples.
- Temperature Control Unit: Maintains a constant environment.
- Waste Management System: Stores alternative solutions for safe disposal.
How a Salt Spray Test Chamber Works
- Specimen Placement: Samples are placed inside the chamber.
- Salt Solution Preparation: A mixture of water and salt is prepared according to test standards.
- Nozzle Activation: The nozzle sprays a fine mist over the samples.
- Controlled Environment: The chamber maintains a set temperature and humidity.
- Evaluation: After testing, samples are examined for signs of corrosion.
Choosing the Right Salt Spray Test Chamber
The selection of an appropriate salt spray chamber depends on factors such as chamber size, spray uniformity, and compliance with ASTM B117 and other test standards.
Preparation Before Installation
Before setting up, ensure:
- The packaging is not damaged.
- The user manual has been thoroughly reviewed.
- All components are intact.
Salt Spray Test Chamber Installation Guide
Choosing the right location
Place the Chamber in a large, well-ventilated area away from direct sunlight or intense heat.
Power Supply and Ventilation Requirements
Make sure the chamber is connected to a stable power source and has adequate ventilation to keep the smoke going.
Connecting the Salt Solution Reservoir
Securely attach the reservoir to prevent leaks during operation.
Setting Up the Test Parameters
- Calibrating Temperature: Adjust according to product specifications.
- Mixing the Solution: Use distilled water and extra pure salt.
- Spray Adjustments: Optimize the nozzle for optimal flooding.
Maintenance Tips for Longevity
- Nozzle Cleaning: Prevent blockages by cleaning nozzles regularly.
- Calibration: Periodic monitoring of temperature and spray stability.
- Inspection: Inspect pipes and valves for leaks or damage.
Common Issues and Troubleshooting
- Uneven Spray Patterns: Clean the spray nozzle and check for blockages.
- Temperature Fluctuations: Check thermostats and power supplies.
- Reservoir Leaks: Tighten connections and check seals.
Safety Tips for Operating a Salt Spray Test Chamber
- Always handle salt solution with care to avoid skin irritation.
- Ensure the chamber has proper ventilation to prevent toxic fume buildup.
Applications of Salt Spray Testing
The salt spray test is widely used in the following ways.
- Automotive Industry: Vehicle parts are tested for corrosion resistance.
- Aerospace and Defense: review of aircraft and safety equipment coverage.
- Marine Applications: To ensure the longevity of ships and offshore facilities.
Future Trends in Salt Spray Testing
- Eco-Friendly Solutions: To minimize the environmental impact of salt spray testing.
- Automation: Smart chambers with HMI-powered controls for precision.
Conclusion
The salt spray test chamber is a cornerstone of optimizing corrosion resistance services. When properly installed, installed, and maintained, these structures can provide accurate, reliable results and ensure product longevity.
FAQs
- What is the standard duration for a salt spray test?
It varies by standard but often ranges from 24 to 1000 hours.
- What is the standard duration for a salt spray test?
- Can I use homemade salt solutions?
It’s recommended to use certified solutions for accurate results.
- Can I use homemade salt solutions?
- How often should I calibrate my chamber?
Calibration should be performed every 6-12 months.
- How often should I calibrate my chamber?
- Is it safe to operate indoors?
Yes, with proper ventilation.
- Is it safe to operate indoors?
- What materials are commonly tested?
Metals, coatings, and polymers are frequently tested.
- What materials are commonly tested?
Leave a Reply