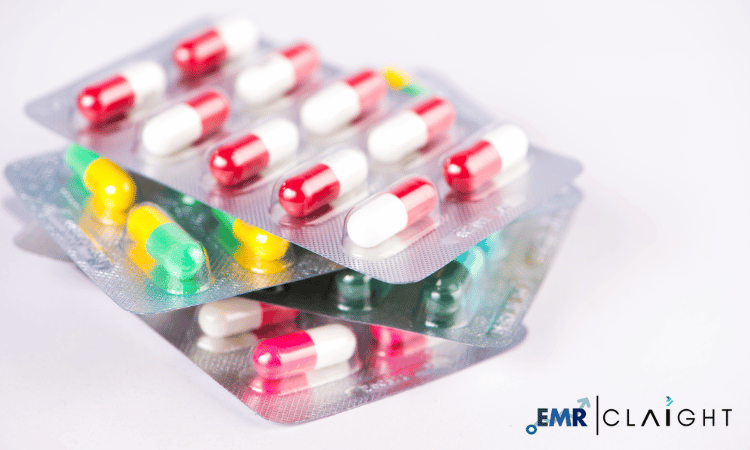
Cefalexin Monohydrate BP is a widely used antibiotic belonging to the cephalosporin family, recognised for its effectiveness in treating a broad spectrum of bacterial infections. Its demand has grown significantly due to its essential role in combating respiratory, skin, and urinary tract infections. As a high-quality pharmaceutical ingredient conforming to British Pharmacopoeia (BP) standards, cefalexin monohydrate is a critical component in healthcare systems worldwide. Establishing a cefalexin monohydrate BP manufacturing plant offers a promising opportunity to cater to the increasing need for effective antibiotics while adhering to stringent quality and regulatory requirements.
Overview of Cefalexin Monohydrate BP
Cefalexin Monohydrate BP is a beta-lactam antibiotic that disrupts bacterial cell wall synthesis, effectively inhibiting the growth of various gram-positive and gram-negative bacteria. It is supplied in crystalline form, primarily used in oral formulations such as capsules, tablets, and suspensions. Its adherence to BP standards ensures its suitability for use in pharmaceutical manufacturing, offering consistent efficacy and safety. As antibiotic resistance continues to pose a global health challenge, cefalexin monohydrate remains a valuable tool in treating bacterial infections.
Get a Free Sample Report with Table of Contents@ https://www.expertmarketresearch.com/prefeasibility-reports/cefalexin-monohydrate-bp-manufacturing-plant-project-report/requestsample
Key Components of a Cefalexin Monohydrate BP Manufacturing Plant
-
Raw Material Procurement
The production of cefalexin monohydrate begins with the acquisition of high-purity raw materials, including starting intermediates and active pharmaceutical ingredients (APIs). Reliable sourcing and quality checks ensure the integrity of the production process. -
Machinery and Equipment
Advanced equipment is crucial for the efficient production of cefalexin monohydrate. Key machinery includes:- Reactors: For chemical synthesis and intermediate reactions.
- Centrifuges: For separation and purification processes.
- Dryers: To obtain the final crystalline form of cefalexin monohydrate.
- Filtration Systems: For removing impurities and ensuring product purity.
- Packaging Machines: For securely sealing the final product.
-
Plant Layout and Design
A well-structured plant layout ensures efficient workflow, with dedicated sections for synthesis, purification, drying, and packaging. Adherence to Good Manufacturing Practices (GMP) and cleanliness standards is critical to maintaining product quality. -
Utilities and Infrastructure
Adequate utilities such as power supply, water, and HVAC systems are essential for plant operations. Water purification systems and waste management infrastructure ensure compliance with environmental regulations. -
Workforce and Training
Skilled personnel are required for operating equipment, monitoring processes, and ensuring quality control. Regular training programs keep the workforce updated on safety protocols and technological advancements.
Manufacturing Process of Cefalexin Monohydrate BP
The production of cefalexin monohydrate involves several stages to ensure high purity and compliance with pharmacopoeial standards:
-
Synthesis
The production begins with the synthesis of cefalexin through a series of controlled chemical reactions. Key intermediates are reacted under specific conditions to form the active compound. -
Purification
The crude product undergoes multiple purification steps, including crystallisation and filtration, to remove impurities and achieve the desired quality. -
Drying
The purified cefalexin is dried using advanced drying systems to obtain the monohydrate form, ensuring proper moisture content and stability. -
Quality Testing
The product is subjected to rigorous quality testing to ensure it meets BP specifications for potency, purity, and stability. -
Packaging
The final product is packaged in airtight containers under sterile conditions to maintain its quality during storage and transportation.
Applications of Cefalexin Monohydrate BP
Cefalexin Monohydrate BP is widely used in pharmaceutical formulations to treat various bacterial infections:
- Respiratory Tract Infections: Effective against conditions such as bronchitis, tonsillitis, and pharyngitis.
- Skin and Soft Tissue Infections: Used to treat cellulitis, abscesses, and wound infections.
- Urinary Tract Infections: Commonly prescribed for cystitis and pyelonephritis.
- Bone and Joint Infections: Plays a role in managing osteomyelitis and septic arthritis.
- Prophylaxis: Administered pre- and post-surgery to prevent bacterial infections.
Market Potential and Demand Drivers
The demand for cefalexin monohydrate is influenced by several factors:
-
Rising Prevalence of Bacterial Infections
The increasing incidence of infections, coupled with growing awareness about early treatment, drives the demand for antibiotics like cefalexin. -
Expanding Pharmaceutical Industry
The global pharmaceutical sectorβs growth, particularly in emerging economies, boosts the need for high-quality APIs. -
Stringent Regulatory Requirements
The emphasis on manufacturing drugs that adhere to BP standards creates a strong market for compliant APIs like cefalexin monohydrate. -
Antibiotic Resistance Management
As healthcare providers focus on using effective antibiotics judiciously, the demand for proven treatments such as cefalexin remains steady.
Challenges in Cefalexin Monohydrate BP Manufacturing
-
Raw Material Costs
Fluctuations in the prices of raw materials and intermediates can impact production costs. Establishing long-term supplier relationships mitigates this risk. -
Regulatory Compliance
Adhering to stringent regulatory standards requires robust quality control systems and regular audits, which can be resource-intensive. -
Process Efficiency
Achieving high yields and consistent product quality demands advanced technology and process optimisation. -
Competition
The market for antibiotics is competitive, requiring differentiation through quality, pricing, and customer service.
Sustainability in Cefalexin Monohydrate BP Manufacturing
Sustainability practices are becoming essential in pharmaceutical manufacturing. Key initiatives include:
- Green Chemistry: Adopting eco-friendly synthesis methods to minimise waste and reduce environmental impact.
- Energy Efficiency: Using energy-efficient equipment to lower operational costs and carbon footprint.
- Waste Management: Implementing systems for recycling and safely disposing of chemical waste.
- Water Conservation: Reducing water usage and investing in purification technologies.
Key Success Factors for a Cefalexin Monohydrate BP Manufacturing Plant
- Quality Assurance: Maintaining consistent quality that meets BP standards is crucial for market acceptance and customer trust.
- Technological Advancements: Investing in state-of-the-art equipment and process optimisation enhances efficiency and competitiveness.
- Regulatory Compliance: Strict adherence to GMP, BP specifications, and environmental regulations ensures smooth operations and market access.
- Market Understanding: Staying informed about industry trends and customer needs helps manufacturers tailor their offerings effectively.
- Sustainability Practices: Incorporating eco-friendly measures strengthens the brandβs reputation and aligns with global initiatives.
By focusing on these aspects, a cefalexin monohydrate BP manufacturing plant can meet the rising demand for high-quality antibiotics while ensuring efficient and sustainable operations.
Leave a Reply