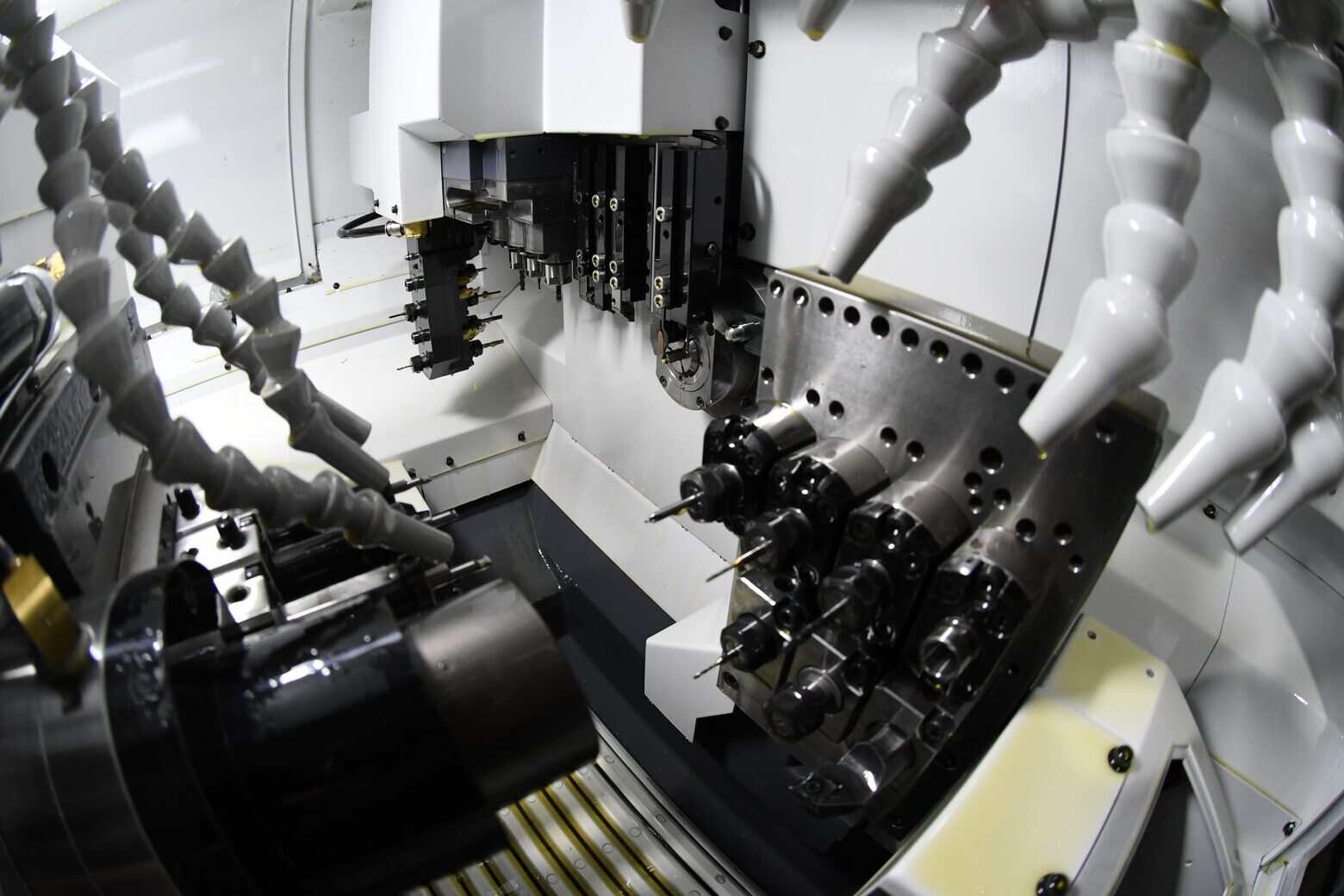
In the fast-evolving medical industry, ensuring the highest standards of precision and quality in manufacturing medical devices is crucial. Whether it’s the creation of delicate surgical tools, life-saving implants, or diagnostic components, CNC machining (Computer Numerical Control machining) is at the heart of producing these critical healthcare products.
Medical CNC enables manufacturers to achieve extraordinary levels of accuracy and efficiency, which are necessary for developing medical devices that meet stringent regulatory standards. The process has transformed how medical devices are created, making them more customized, reliable, and cost-effective. This article delves into the significance of CNC machining in the medical field, its advantages, applications, and how it continues to shape the future of healthcare manufacturing.
What is CNC Machining?
CNC machining is a manufacturing process where computers control machine tools such as mills, lathes, and routers to shape material into precise parts. In the context of the medical industry, CNC machining is used to produce high-quality parts, ranging from intricate surgical instruments to prosthetic limbs. The process involves a digital design (often created using CAD software) that is translated into machine language by CAM (Computer-Aided Manufacturing) software.
CNC machines are capable of working with various materials commonly used in medical device production, such as stainless steel, titanium, plastics, ceramics, and other biocompatible materials. The machines operate with incredible precision, ensuring that every part is manufactured to exact specifications, making them safe and reliable for use in medical treatments.
The Role of CNC in the Medical Industry
The primary role of CNC machining in the medical industry is to create parts and components with the precision and repeatability required for medical applications. Whether itโs creating surgical tools, custom implants, or orthopedic devices, CNC technology ensures that every product is made to the exact tolerances necessary for patient safety and optimal functionality.
Key Benefits of CNC Machining in the Medical Industry
CNC machining offers several advantages that are critical for the production of medical devices. These benefits are driving the widespread adoption of CNC machining technology across the healthcare sector.
1. High Precision and Accuracy
One of the main reasons CNC machining is indispensable in the medical industry is its unparalleled precision. Medical devices require extremely tight tolerancesโsometimes as small as a few micrometers. CNC machines can produce components with exact measurements, ensuring that parts fit together perfectly and function as intended. Whether itโs a tiny surgical tool or a complex implant, CNC machining guarantees that every detail is precisely executed.
2. Customization and Personalization
Medical devices often need to be tailored to individual patients, especially in cases like implants and prosthetics. CNC machining is ideal for creating custom medical solutions. Implants and prosthetic limbs can be designed based on the exact measurements of a patientโs body, ensuring a better fit and higher success rates. For example, custom knee replacements, dental implants, and even facial implants can be made with CNC machines, resulting in better outcomes for patients.
3. Complex Designs Made Possible
Many medical devices have intricate geometries and features that would be impossible to manufacture with traditional methods. CNC machines are capable of executing complex cuts, curves, and detailed patterns, allowing manufacturers to create components with complex shapes that are essential for modern medical devices. This flexibility is particularly important for medical devices such as surgical tools, diagnostic equipment, and implants.
4. Material Versatility
CNC machines can handle a wide variety of materials, including metals like stainless steel and titanium, which are often used in medical devices due to their biocompatibility and durability. Additionally, plastics, ceramics, and specialized composites can also be used, depending on the requirements of the device. The ability to work with diverse materials makes CNC machining a go-to process in the production of medical components.
5. Consistency and Reproducibility
CNC machining is automated, which means it can produce identical parts with the same level of precision each time. This consistency is vital in the medical field, where even small deviations from the design can result in compromised performance and safety risks. Manufacturers rely on CNC machines to produce large batches of parts that meet the exact same specifications every time, reducing human error and ensuring a high level of quality.
6. Faster Production Times
CNC machining is a highly efficient process. Once the program is set up, the machines can work continuously with minimal intervention, leading to faster turnaround times. In the fast-paced medical industry, manufacturers need to produce medical devices quickly without compromising quality. CNC machining helps meet this demand by speeding up production times and improving efficiency.
Applications of CNC Machining in the Medical Field
CNC machining is used in a wide array of applications in the medical industry. Here are some of the key areas where CNC technology is making a significant impact:
1. Surgical Instruments
Surgical instruments, such as scalpels, forceps, and scissors, require extremely precise manufacturing. CNC machines can produce these instruments with tight tolerances, ensuring they function reliably and safely during surgeries. Additionally, CNC machines can create ergonomic designs for tools, making them easier for surgeons to handle during procedures.
2. Implants and Prosthetics
CNC machining is used to create a variety of implants, such as hip replacements, knee implants, dental implants, and spinal components. These implants must meet precise specifications to ensure proper fit and functionality within the human body. CNC technology allows for the creation of custom implants tailored to the patientโs anatomy, improving the chances of a successful treatment. Prosthetics, including artificial limbs, can also be customized using CNC machining to ensure a perfect fit.
3. Orthopedic Devices
Orthopedic devices, such as bone plates, screws, and spinal implants, often require high strength and durability. CNC machines are used to manufacture these components with exceptional precision, ensuring that they fit the patient’s body correctly and perform well under stress. These devices are critical for treating fractures, joint replacements, and spinal conditions, and CNC machining guarantees their reliability.
4. Dental Components
CNC machining has transformed the dental industry by enabling the creation of custom dental components such as crowns, bridges, dentures, and orthodontic devices. Dentists rely on CNC machines to create components that fit the patientโs mouth precisely, ensuring comfort and effectiveness. Additionally, CNC machines can be used to create materials that mimic the appearance of natural teeth, improving the aesthetic quality of dental devices.
5. Medical Equipment Parts
Beyond devices directly involved in patient care, CNC machining is also used to produce parts for medical diagnostic and imaging equipment. For example, components of MRI machines, X-ray devices, and CT scanners require precision to ensure they work correctly and consistently. CNC machines can produce the intricate and often small components that these machines need to function efficiently.
6. Micro-Surgical Devices
In the realm of micro-surgery, where highly specialized and delicate instruments are used, CNC machining plays a vital role in manufacturing the precise tools required. These include fine-tipped forceps, scalpels, and other instruments used in eye surgery, neurological procedures, and minimally invasive surgeries. CNC machines allow for the production of these micro devices with the exact dimensions required.
The Future of CNC Machining in the Medical Industry
As technology continues to evolve, CNC machining in the medical field is poised for further innovation. 3D printing is beginning to complement traditional CNC machining, offering even more customization possibilities and faster prototyping. For example, in the creation of patient-specific implants, 3D printing and CNC machining can work together to deliver personalized, complex solutions quickly and efficiently.
Additionally, multi-axis CNC machines are becoming more advanced, allowing for even greater complexity and precision in medical device manufacturing. With developments in automation and artificial intelligence, the future of CNC machining holds even more promise for improving the quality, customization, and efficiency of medical devices.
Conclusion
CNC machining is a game-changer for the medical industry, enabling manufacturers to produce parts and devices with unmatched precision, consistency, and customization. From surgical tools and implants to diagnostic equipment and orthopedic devices, CNC technology is revolutionizing how medical products are made. As the demand for high-quality, patient-specific medical solutions continues to grow, CNC machining will play an even more pivotal role in advancing the healthcare industry.
By improving the accuracy, reliability, and speed of production, CNC machining helps ensure that patients receive the best possible care through the use of state-of-the-art medical devices. The future of healthcare manufacturing is bright, and CNC machining will undoubtedly remain at the forefront of this transformation.
Leave a Reply