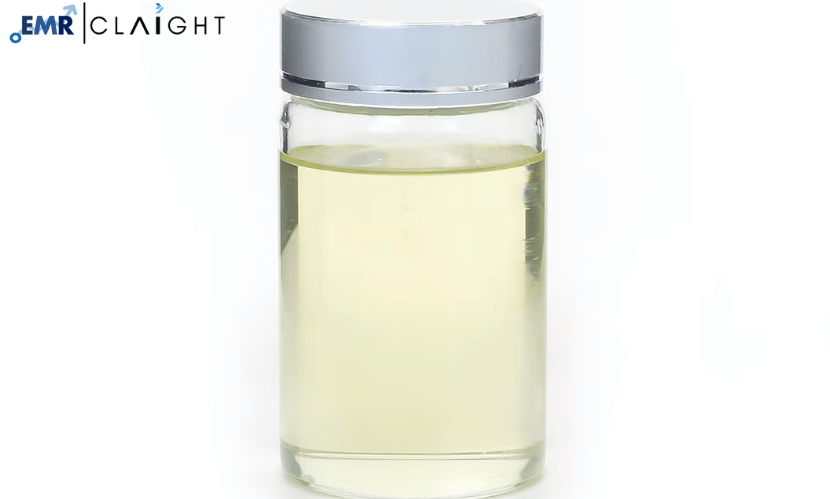
N-Methyl Aniline (NMA) is a versatile organic compound extensively used in the production of dyes, pesticides, and as an additive in fuels. Its chemical properties make it an indispensable ingredient in the manufacture of high-performance industrial and agricultural products. Setting up an N-Methyl Aniline manufacturing plant requires precision in chemical processes, adherence to environmental and safety standards, and efficient operational practices. This article provides a detailed guide on the production methods, equipment, and considerations for establishing a successful N-Methyl Aniline production facility.
Understanding N-Methyl Aniline
N-Methyl Aniline is a derivative of aniline, distinguished by its additional methyl group. It is primarily used as an intermediate in dye synthesis, fuel additives, and certain agrochemical formulations. Its ability to enhance octane levels in fuels and its significance in industrial applications underline its demand across various markets.
Get a Free Sample Report with Table of Contents@ https://www.expertmarketresearch.com/prefeasibility-reports/n-methyl-aniline-manufacturing-plant-project-report/requestsample
Key Processes in Manufacturing
- Raw Material Preparation
- Aniline and methylating agents are the primary raw materials used in the synthesis of N-Methyl Aniline. These materials undergo quality checks to ensure compliance with industry standards.
- Methylation Reaction
- The manufacturing process involves the controlled reaction of aniline with a methylating agent. This reaction is conducted under specific temperature and pressure conditions to maximise yield and purity.
- Separation and Purification
- The reaction mixture is processed to separate N-Methyl Aniline from by-products. Purification techniques, such as distillation, are employed to achieve the desired product quality.
- Quality Testing
- The purified N-Methyl Aniline is subjected to rigorous quality testing to ensure compliance with industrial specifications for purity, stability, and reactivity.
- Packaging and Storage
- The final product is packaged in chemical-grade containers to preserve its quality and is stored under controlled conditions to ensure safety.
Essential Equipment for a Manufacturing Plant
Setting up an N-Methyl Aniline manufacturing plant requires advanced equipment for safe and efficient production. Key equipment includes:
- Reactors: For conducting methylation reactions under controlled conditions.
- Distillation Units: For purifying the final product by separating impurities and by-products.
- Mixing Tanks: For blending raw materials and intermediate compounds.
- Quality Testing Instruments: For analysing the purity, stability, and other properties of N-Methyl Aniline.
- Storage Tanks: For safely storing raw materials and the final product.
- Packaging Machines: For sealing and labelling containers with the finished product.
Designing the Plant Layout
An efficient plant layout ensures streamlined production and compliance with safety standards. Key considerations include:
- Raw Material Storage: Dedicated areas for securely storing aniline and methylating agents.
- Processing Zones: Separate sections for methylation reactions, purification, and quality control.
- Quality Control Laboratory: Equipped for testing raw materials and the final product.
- Packaging and Storage Areas: Facilities for securely packaging and storing N-Methyl Aniline.
- Waste Management Systems: For treating and disposing of by-products in an environmentally friendly manner.
Quality Control in Manufacturing
Maintaining consistent quality is critical in N-Methyl Aniline production. Key quality control practices include:
- Raw Material Testing: Verifying the purity and quality of aniline and methylating agents.
- Process Monitoring: Ensuring optimal reaction conditions, such as temperature and pressure.
- Product Testing: Assessing the purity, stability, and reactivity of the final product.
- Packaging Inspection: Ensuring containers are sealed securely and labelled with safety information.
Regulatory and Licensing Requirements
Setting up an N-Methyl Aniline manufacturing plant involves adhering to strict safety and environmental regulations. Key requirements include:
- Chemical Safety Certifications: Compliance with standards for handling and storing hazardous chemicals.
- Environmental Clearances: Managing emissions, waste, and effluents responsibly to minimise environmental impact.
- Labelling Compliance: Providing accurate information about the productβs properties and safety precautions.
- Workplace Safety Regulations: Ensuring the safety of workers through training and proper handling protocols.
Applications of N-Methyl Aniline
N-Methyl Aniline is a highly versatile compound with applications in various industries:
- Dye Industry: Used as an intermediate in the synthesis of high-performance dyes and pigments.
- Fuel Additives: Incorporated into fuels to improve octane ratings and enhance performance.
- Agrochemicals: A key ingredient in the production of pesticides and herbicides.
- Pharmaceuticals: Employed as an intermediate in certain drug formulations.
- Specialty Chemicals: Used in the production of customised industrial compounds.
Sustainability in Manufacturing
Sustainability is a key focus in N-Methyl Aniline production. Measures to enhance sustainability include:
- Efficient Resource Utilisation: Optimising raw material usage to minimise waste.
- Emission Control: Implementing scrubbers and filters to reduce harmful emissions.
- Recycling By-Products: Developing systems to repurpose waste materials into useful products.
- Energy Efficiency: Employing energy-saving technologies in reactors and purification systems.
Market Trends and Opportunities
The demand for N-Methyl Aniline is growing due to its widespread applications across industries. Key trends include:
- Expansion in the Dye Industry: Rising demand for high-performance dyes drives the need for intermediates like N-Methyl Aniline.
- Growth in Fuel Additives: Increased adoption of fuel additives to meet regulatory standards for cleaner emissions.
- Sustainability Focus: Development of eco-friendly production methods to reduce the environmental impact.
- Global Market Growth: Higher adoption in emerging markets driven by industrialisation and urbanisation.
Challenges in the industry include:
- Regulatory Compliance: Navigating strict environmental and safety standards.
- Market Competition: Differentiating products through innovation and consistent quality.
- Raw Material Costs: Managing fluctuations in the prices of aniline and methylating agents.
By leveraging advanced production techniques, ensuring stringent quality control, and embracing sustainable practices, manufacturers can establish a successful N-Methyl Aniline production facility to meet the growing global demand across industries.
Leave a Reply