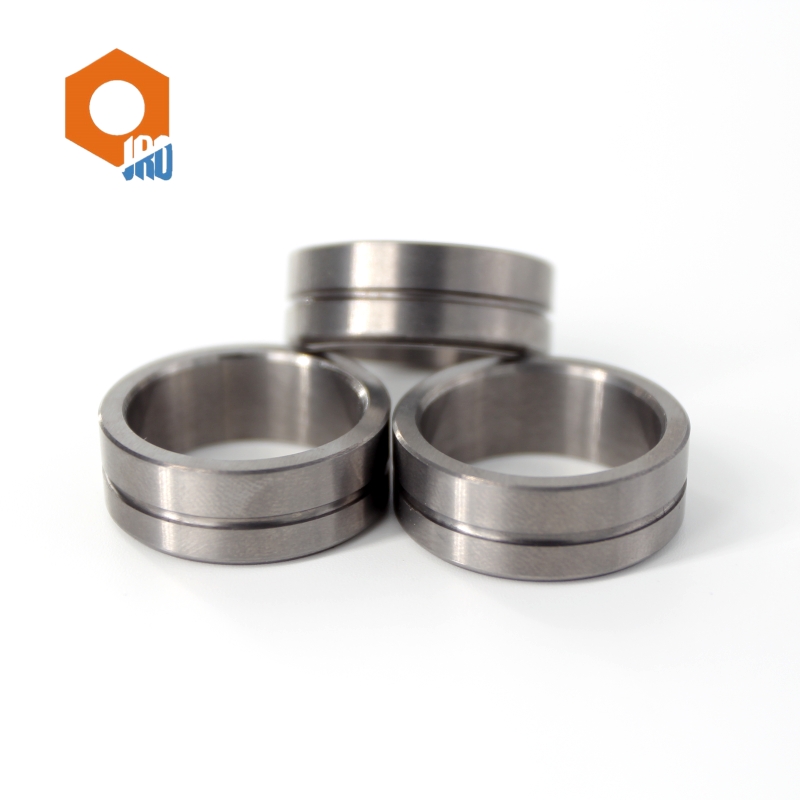
In industries like mining, construction, and heavy manufacturing, equipment efficiency and reliability are crucial. The constant exposure to abrasive materials, extreme pressures, and harsh operating conditions takes a toll on machinery, often leading to downtime and increased maintenance costs. Custom carbide wear parts have emerged as a transformative solution, providing tailored durability and precision that optimize equipment performance. This article explores how custom carbide wear parts enhance equipment efficiency, reduce operational costs, and extend the life of machinery.
1. The Importance of Wear Parts in Industrial Equipment
Wear parts play a vital role in maintaining the functionality of industrial equipment. These components endure constant friction, impact, and erosion during operations, making them prone to wear and tear.
- Definition: Wear parts are replaceable components that absorb the brunt of wear in machinery.
- Common Examples: Drill bits, crusher teeth, pump linings, and cutting tools.
- Significance: High-quality wear parts are essential for ensuring consistent equipment performance and minimizing downtime.
2. Why Choose Custom Carbide Wear Parts?
Carbide wear parts, made primarily of tungsten carbide, are known for their unparalleled hardness and toughness. Customizing these parts allows them to meet specific operational requirements, offering several advantages over standard wear parts.
- Tailored Design: Customization ensures the wear parts fit precisely into machinery and align with operational needs.
- Material Optimization: Adjusting carbide grain size, binder composition, and coatings enhances wear resistance and toughness for specific applications.
- Result: Superior performance, reduced wear, and longer lifespan for machinery components.
3. Enhanced Durability for High-Stress Applications
In industries like mining and oil drilling, equipment is exposed to high-stress conditions, including impact, abrasion, and thermal stress. Custom carbide wear parts are designed to withstand these challenges.
- Key Features:
- High resistance to abrasion and impact.
- Retention of structural integrity under extreme pressures and temperatures.
- Example: Customized carbide crusher teeth in mining equipment resist the abrasive forces of hard minerals, reducing the frequency of part replacements.
4. Precision Fit for Improved Equipment Efficiency
Off-the-shelf wear parts may not always provide the perfect fit for specific machinery, leading to inefficiencies and increased wear. Custom carbide wear parts, however, are engineered to match exact specifications.
- Advantages:
- Better alignment reduces mechanical stress on adjacent components.
- Improved energy efficiency due to reduced friction and wear.
- Case Study: A manufacturing plant using custom carbide cutting tools achieved a 20% increase in production efficiency by eliminating tool misalignment.
5. Extended Equipment Lifespan
Carbide wear parts not only enhance the durability of the parts themselves but also protect the equipment from excessive wear.
- Mechanism: By reducing friction, impact, and erosion on critical machinery surfaces, custom carbide parts prevent damage to the main equipment structure.
- Outcome: Extended lifespan of the entire system, reducing long-term replacement and repair costs.
- Industry Example: Heavy-duty conveyors in mining operations equipped with custom carbide-lined wear plates experienced a 50% increase in operational life.
6. Reduced Downtime and Maintenance Costs
Frequent part replacements and unplanned maintenance can significantly disrupt operations and increase costs. Custom carbide wear parts address this issue by lasting longer and requiring less frequent maintenance.
- Impact on Operations:
- Minimized downtime for part replacement or repair.
- Reduced inventory requirements for spare parts.
- Example: Oil and gas companies using custom carbide seals and valves reported a 30% reduction in maintenance downtime, enhancing overall productivity.
7. Application-Specific Customization for Optimal Performance
Different industries and applications present unique challenges that standard wear parts cannot address effectively. Custom carbide wear parts are designed to tackle these specific issues.
- Examples of Custom Applications:
- Mining: Carbide-tipped drill bits for cutting through hard rock formations.
- Construction: Custom carbide blades for asphalt and concrete cutting.
- Oil and Gas: Carbide nozzles for abrasive fluid handling.
- Benefit: Application-specific customization ensures optimal performance under diverse operational conditions.
8. Cost-Effectiveness Over the Long Term
Although custom carbide wear parts have a higher upfront cost than standard options, their long-term benefits far outweigh the initial investment.
- Cost Savings:
- Lower frequency of replacements reduces material costs.
- Enhanced efficiency minimizes energy consumption.
- Extended equipment life reduces capital expenditures on new machinery.
- Conclusion: Custom carbide wear parts deliver significant cost savings over time, making them a strategic investment.
9. Supporting Sustainability Goals
Custom carbide wear parts align with sustainability efforts by reducing waste and improving resource efficiency.
- Environmental Benefits:
- Fewer replacements generate less waste.
- Reduced energy consumption lowers carbon emissions.
- Example: A mining company using custom carbide parts in crushers reduced its waste output by 15% due to the longer lifespan of components.
10. Innovations in Custom Carbide Wear Parts
Advancements in carbide technology continue to improve the performance of custom wear parts.
- Emerging Trends:
- Nano-grain carbide for enhanced toughness and wear resistance.
- Advanced coatings for superior corrosion protection.
- Integration of smart sensors to monitor wear and predict maintenance needs.
- Future Outlook: These innovations will further enhance the ability of custom carbide wear parts to optimize equipment performance.
Conclusion
Carbide wear parts have revolutionized equipment performance in industries where durability, precision, and efficiency are critical. By tailoring wear parts to specific applications, businesses can enhance productivity, reduce maintenance costs, and extend the lifespan of machinery. The long-term benefits of custom carbide solutions make them an indispensable investment for industries seeking to optimize their operations and achieve sustainable growth. As technology continues to advance, the role of custom carbide wear parts in industrial equipment optimization will only grow stronger.
Leave a Reply