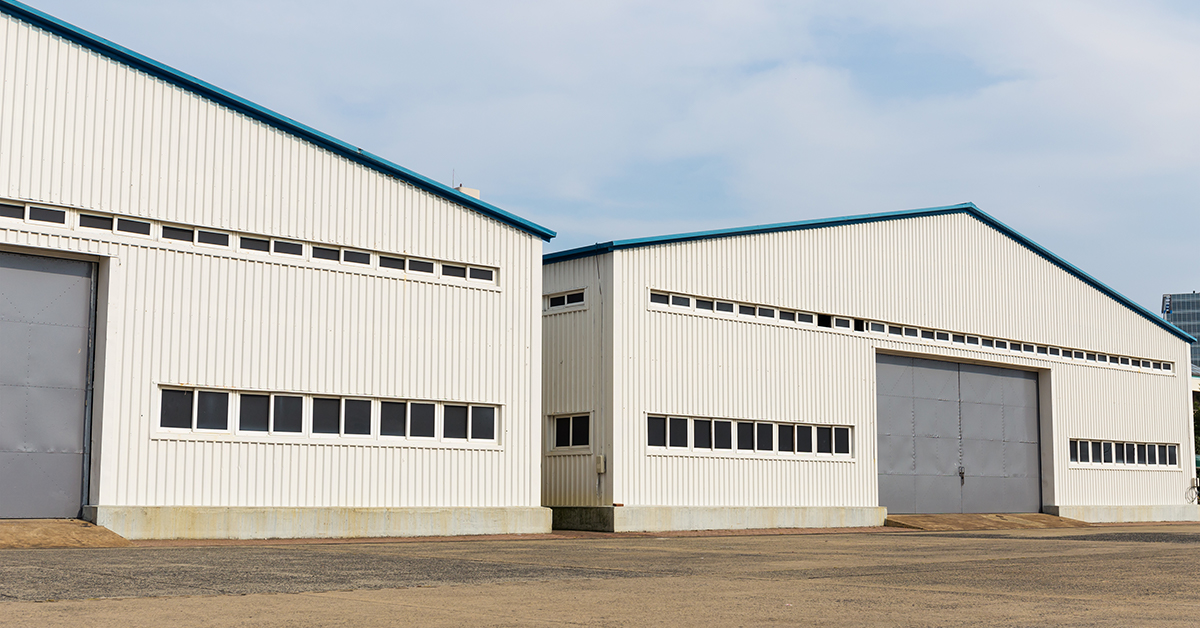
In recent years, the construction industry has witnessed a dramatic shift with the advent of prefabricated warehouse manufacturing. Traditional warehouse construction, with its lengthy timelines and high costs, is being gradually replaced by more efficient and cost-effective methods, offering a quicker and more streamlined approach to building.
Prefabricated warehouse manufacturing not only promises speed but also delivers on quality, sustainability, and customization, making it a game-changer for businesses in need of large-scale storage solutions. In this blog, we’ll explore the world of prefabricated warehouse construction, its key advantages, its impact on the industry, and what the future holds for this transformative technology.
What is Prefabricated Warehouse Manufacturing?
Prefabricated warehouse manufacturing refers to the process of constructing the components of a warehouse off-site in a factory-controlled environment, then transporting these components to the construction site for assembly. Unlike traditional construction, where everything is built from scratch on-site, prefabricated structures are designed, engineered, and partially built in factories.
This process typically involves creating standardized building modules—such as walls, roofing, and structural supports—that can be quickly assembled upon delivery. Prefabrication allows for high precision, as factory environments offer controlled conditions that are less affected by weather or other external factors that could cause delays in traditional construction projects.
Key Advantages of Prefabricated Warehouses
The shift toward prefabrication in industrial warehouse construction services is largely driven by several key advantages. Below, we break down the benefits that are prompting more businesses to adopt this modern approach.
1. Speed of Construction
- Faster Project Completion: Prefabrication significantly reduces construction time as most components are built off-site and delivered ready for assembly.
- Reduced Downtime: By preparing components in advance, businesses experience less downtime, ensuring they can begin operations sooner than they would with traditional construction.
2. Cost Efficiency
- Lower Labor Costs: Since much of the work is done off-site, there is a reduced need for on-site labor, which often drives down costs.
- Minimized Material Waste: In a controlled factory setting, materials are measured and cut with precision, reducing waste and the expense that comes with it.
- Streamlined Construction Process: With less time spent on-site, ancillary costs such as logistics and supervision are also lower.
3. Flexibility and Customization
- Adaptability to Business Needs: Prefabricated warehouses can be tailored to fit the specific needs of businesses, allowing for custom designs that enhance operational efficiency.
- Scalability: These warehouses can be easily expanded as a company grows, with additional modules or sections added as needed.
- Modular Design: The modular nature of prefabricated warehouses makes them versatile, allowing businesses to modify and adapt layouts quickly.
4. Enhanced Quality Control
- Controlled Environment: Factory-built components benefit from a controlled manufacturing process, ensuring high-quality production standards and reducing human error.
- Weather-Protected Construction: Unlike traditional construction, which can face delays and quality issues due to adverse weather conditions, prefabrication occurs in sheltered environments, safeguarding materials and workmanship.
5. Sustainability
- Reduced Material Waste: The precision of prefabrication processes leads to less material waste, contributing to more eco-friendly construction practices.
- Energy Efficiency: Prefabricated warehouses are designed to be energy-efficient, with improved insulation and sustainable materials often incorporated into the design.
- Green Building Practices: Many companies in prefabrication are adopting green building standards, using recycled materials and implementing waste-reduction strategies.
Impact on the Supply Chain and Logistics Industry
The rise of prefabricated warehouse manufacturing is having a profound effect on the supply chain and logistics sectors. These industries rely on efficient warehouse spaces to ensure smooth operations, and prefabrication offers several benefits that make it an attractive solution for businesses aiming to streamline their logistics.
1. Meeting the Growing Demand for Warehousing
As the e-commerce boom continues, companies are in constant need of additional storage space. Prefabricated warehouse construction allows businesses to meet these demands quickly, enabling them to expand their operations without extended delays.
2. Faster Deployment of Warehouses
With the rapid construction timelines associated with prefabrication, companies in the logistics sector can quickly establish new storage facilities. This is crucial for companies needing to keep pace with market changes and consumer demand.
3. Improved Operational Efficiency
By utilizing prefabricated warehouses, logistics companies can optimize their space for specific functions, such as order fulfillment or bulk storage. Custom designs ensure that these warehouses are built with efficiency in mind, improving workflow and reducing operational costs.
Trends Driving the Adoption of Prefabricated Warehouses
Several emerging trends are contributing to the increased adoption of prefabricated warehouse construction services. These trends reflect both technological advancements and a shift toward more sustainable and efficient building practices.
1. Technological Advancements
- Automation in Prefabrication: New technologies such as robotics, automation, and computer-aided design (CAD) systems have revolutionized the prefabrication process. These advancements enable manufacturers to produce warehouse components with higher accuracy and speed.
- Smart Warehousing: Prefabricated warehouses can easily integrate smart technologies, such as the Internet of Things (IoT) and automated storage systems. These technologies enhance warehouse operations, providing real-time monitoring and management capabilities.
2. Increasing Demand for Warehousing Space
- E-commerce Growth: With the rapid rise of e-commerce, businesses are constantly seeking ways to expand their storage capacity. Prefabricated warehouses offer a fast and flexible solution to accommodate this growing need.
- Just-in-Time (JIT) Logistics: Many businesses are adopting JIT logistics practices, which require readily available storage spaces that can be deployed quickly. Prefabricated warehouses meet these demands by providing fast construction timelines and scalable solutions.
3. Sustainability Initiatives
- Green Construction Practices: The focus on sustainability in construction is growing, and prefabrication aligns with this trend. Many prefabricated warehouse manufacturers use sustainable materials, energy-efficient designs, and waste-reduction strategies in their processes.
- LEED-Certified Warehouses: Companies are increasingly seeking LEED (Leadership in Energy and Environmental Design) certification for their facilities. Prefabricated warehouses can be designed to meet these environmental standards, contributing to greener operations.
Success Stories in Prefabricated Warehouse Manufacturing
To illustrate the impact of prefabricated warehouse manufacturing, let’s look at a few success stories from businesses that have adopted this approach.
1. A Leading Logistics Company
A global logistics firm needed to rapidly expand its warehouse footprint due to rising demand. By opting for prefabricated warehouse solutions, the company was able to complete construction in half the time of traditional methods, saving both time and money.
2. A Growing Manufacturing Business
A mid-sized manufacturer sought to increase its production capacity by adding new storage space. Prefabricated warehouse manufacturing allowed the company to customize its layout, incorporating specialized storage areas and improving operational efficiency.
3. A Major Retailer
An international retailer faced challenges with traditional construction timelines when trying to expand its distribution centers. Prefabricated warehouses provided a solution, enabling them to roll out new facilities quickly while keeping costs under control.
Challenges and Limitations of Prefabricated Warehouses
While prefabricated warehouse construction offers many advantages, there are a few challenges that businesses should be aware of.
1. Design Limitations
- Standardization vs. Customization: Prefabricated warehouses may face limitations in terms of design flexibility compared to traditional construction. Businesses with highly specific needs may find that prefabrication doesn’t always allow for complete customization.
2. Transportation Logistics
- Delivery of Prefabricated Components: Transporting large prefabricated components to the construction site can be challenging, particularly if the site is in a remote location. This can add logistical complexities and potential delays to the process.
3. Regulatory Hurdles
- Local Building Codes: Some regions may have strict building codes and regulations that could complicate the installation of prefabricated structures. It’s important to ensure compliance with local laws and requirements before opting for this construction method.
The Future of Prefabricated Warehouse Manufacturing
Looking ahead, the future of prefabricated warehouse manufacturing appears bright, with several exciting developments on the horizon.
1. Emerging Technologies
- 3D Printing: Advances in 3D printing technology may soon play a role in the prefabrication process, allowing for even greater precision and customization.
- Modular Construction: Modular construction is gaining popularity, enabling businesses to create large-scale warehouse facilities by combining prefabricated modules. This approach allows for greater flexibility and scalability.
2. Industry Growth
As more businesses recognize the benefits of prefabricated construction, the demand for these solutions is expected to rise. The best warehouse construction company will continue to innovate, offering advanced solutions that cater to the evolving needs of the industry.
Conclusion
Prefabricated warehouse manufacturing is changing the landscape of industrial warehouse construction services by providing faster, more cost-effective, and sustainable solutions. From reducing construction time to offering customizable and scalable options, this approach is becoming the preferred choice for businesses in need of new warehouse facilities. As technology continues to advance and demand for storage space grows, prefabrication will play an even greater role in shaping the future of construction. Businesses looking to stay competitive in a fast-paced market should consider the numerous benefits that prefabricated warehouses can offer.
Leave a Reply