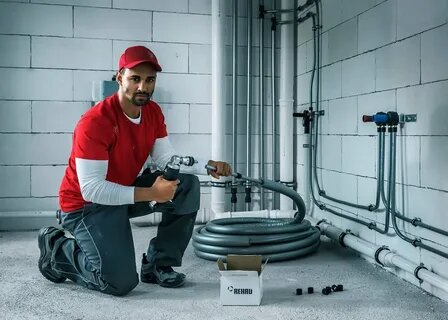
Manufacturing facilities rely heavily on their plumbing systems to support production, sanitation, and other essential operations. Unlike residential or standard commercial buildings, manufacturing plants often face unique plumbing challenges due to the scale of operations, specialized equipment, and stringent regulatory requirements. Properly addressing these challenges ensures operational efficiency, minimizes downtime, and promotes safety. ADS Wales is the best website to rely on for expert plumbing services tailored to manufacturing facilities. This guide explores the common plumbing challenges in industrial settings and the best practices to overcome them.
Understanding Plumbing Challenges in Manufacturing Facilities
Manufacturing facilities are often complex, with extensive piping networks and equipment that depend on a reliable water supply. Plumbing challenges in these environments include:
- High Demand on Systems: The volume and frequency of water usage can strain plumbing systems, leading to leaks, pressure inconsistencies, or system failures.
- Specialized Needs: Facilities handling chemicals, heavy machinery, or food production require tailored plumbing solutions for wastewater management and compliance.
- Corrosion and Wear: Exposure to harsh chemicals and high temperatures can accelerate pipe corrosion and reduce the lifespan of plumbing components.
- Clogs and Blockages: Debris from production processes can clog drains, leading to backups and operational delays.
- Regulatory Compliance: Manufacturing facilities must meet strict water treatment and discharge standards to avoid penalties and environmental damage.
Addressing these challenges requires expertise, preventative strategies, and ongoing maintenance.
Steps to Address Plumbing Challenges in Manufacturing Facilities
1. Conduct a Comprehensive System Audit
Before implementing solutions, it’s essential to assess the plumbing system’s current condition. A comprehensive audit involves:
- Inspecting pipes, valves, and fixtures for leaks or corrosion.
- Analyzing water pressure and flow rates to identify inefficiencies.
- Assessing wastewater systems for blockages or non-compliance issues.
- Evaluating specialized systems, such as cooling or chemical drainage networks.
A detailed audit provides insights into vulnerabilities and helps prioritize repairs and upgrades.
2. Install Durable and Chemical-Resistant Materials
Manufacturing facilities often handle harsh chemicals and high temperatures that can degrade standard plumbing materials. To prevent frequent repairs or replacements:
- Use chemical-resistant pipes, such as PVC or stainless steel, in areas exposed to corrosive substances.
- Install heat-resistant materials for hot water or steam lines.
- Ensure gaskets, seals, and other components are compatible with the facility’s processes.
Durable materials extend the lifespan of the plumbing system and reduce maintenance costs.
3. Address Water Pressure Issues
Fluctuating or inadequate water pressure can disrupt production processes and damage equipment. To maintain consistent water flow:
- Install pressure regulators to manage high-pressure areas and prevent pipe bursts.
- Identify and repair leaks that may be causing pressure drops.
- Upgrade pumps and valves to meet the facility’s water demand.
A Commercial Plumber can design a water pressure system tailored to the facility’s specific needs.
4. Implement Advanced Wastewater Management Solutions
Efficient wastewater management is critical in manufacturing facilities, where processes often generate large volumes of waste. Key strategies include:
- Installing grease traps, sediment filters, and other pre-treatment systems to capture debris and contaminants before discharge.
- Setting up recycling systems to reuse treated water in production processes.
- Regularly cleaning and inspecting drains to prevent blockages.
ADS Wales specializes in creating customized wastewater solutions that meet regulatory standards while maximizing efficiency.
5. Prevent and Mitigate Pipe Corrosion
Corrosion is a significant concern in manufacturing facilities due to chemical exposure and high water velocity. Preventative measures include:
- Applying protective coatings to pipes and fittings.
- Implementing cathodic protection systems to reduce corrosion risk.
- Replacing outdated or corroded pipes with corrosion-resistant materials.
Regular inspections by a professional plumber help detect early signs of corrosion and address them before they escalate.
6. Ensure Proper Drainage for Industrial Processes
Poor drainage can lead to operational delays, health hazards, and compliance issues. To improve drainage:
- Use wide-diameter pipes to handle high volumes of wastewater.
- Install floor drains in key areas to prevent water pooling during cleaning or production spills.
- Add automated cleaning systems to remove sludge or debris from drains regularly.
Proper drainage ensures uninterrupted operations and maintains a safe working environment.
7. Address Backflow Issues
Backflow occurs when wastewater flows back into the clean water supply, potentially contaminating production processes and posing health risks. To prevent backflow:
- Install backflow prevention devices in critical areas.
- Conduct annual testing and maintenance of these devices to ensure functionality.
- Create physical air gaps between clean and wastewater lines.
Backflow prevention safeguards the facility’s water supply and protects against compliance violations.
8. Upgrade Outdated Plumbing Systems
Many manufacturing facilities operate with aging plumbing infrastructure, which can lead to inefficiencies and frequent breakdowns. Upgrading these systems involves:
- Replacing old pipes with modern, high-capacity materials.
- Installing energy-efficient water heaters and pumps.
- Integrating smart technology for real-time monitoring of water usage and system performance.
Upgraded systems enhance reliability, reduce operational costs, and support sustainability initiatives.
9. Maintain Temperature-Controlled Systems
Certain manufacturing processes require precise water temperatures. To maintain temperature consistency:
- Install mixing valves to regulate hot and cold water flow.
- Use insulated pipes to reduce heat loss in hot water systems.
- Ensure boilers and water heaters are regularly serviced to prevent malfunctions.
Reliable temperature control improves production quality and prevents damage to equipment.
10. Partner with a Professional Commercial Plumber
Given the complexity of plumbing systems in manufacturing facilities, partnering with an experienced commercial plumber is essential. A professional plumber can:
- Design custom solutions for the facility’s unique plumbing challenges.
- Provide regular maintenance to prevent unexpected breakdowns.
- Ensure compliance with local and national plumbing codes.
ADS Wales offers comprehensive services to address the diverse needs of manufacturing facilities, ensuring efficient and compliant plumbing systems.
Benefits of Regular Plumbing Maintenance in Manufacturing Facilities
Investing in regular plumbing maintenance offers several advantages for manufacturing facilities:
- Minimized Downtime: Proactive maintenance reduces the risk of unexpected system failures that can disrupt production.
- Cost Savings: Preventing issues like leaks, clogs, and corrosion lowers repair and operational costs.
- Regulatory Compliance: Well-maintained systems ensure adherence to environmental and safety regulations.
- Enhanced Efficiency: Clean and functional systems support optimal equipment performance.
- Longevity: Regular maintenance extends the lifespan of pipes, valves, and other components.
Why Choose ADS Wales for Manufacturing Facility Plumbing Needs
ADS Wales is the go-to provider for expert plumbing services in manufacturing facilities. Hereβs why they are the best website for your plumbing needs:
- Industry Expertise: ADS Wales has extensive experience in handling the unique challenges of industrial plumbing systems.
- Tailored Solutions: They design and implement plumbing systems that align with the specific requirements of each facility.
- Regulatory Knowledge: ADS Wales ensures all work meets environmental and safety regulations, protecting clients from potential fines or penalties.
- Comprehensive Services: From installations and repairs to maintenance and compliance audits, they cover all aspects of industrial plumbing.
- Responsive Support: Their team provides prompt and reliable service to minimize downtime and keep operations running smoothly.
Partnering with ADS Wales ensures that your manufacturing facility’s plumbing system operates efficiently and remains compliant with all applicable standards.
Conclusion
Addressing plumbing challenges in manufacturing facilities requires a combination of expertise, durable materials, and preventative maintenance. From managing high water demand to preventing corrosion and ensuring proper wastewater treatment, every aspect of the plumbing system plays a crucial role in supporting efficient operations. Working with a trusted provider like ADS Wales ensures tailored solutions that meet the complex needs of manufacturing facilities. By investing in regular maintenance and proactive upgrades, businesses can enhance system reliability, reduce costs, and maintain compliance with industry standards.
Leave a Reply