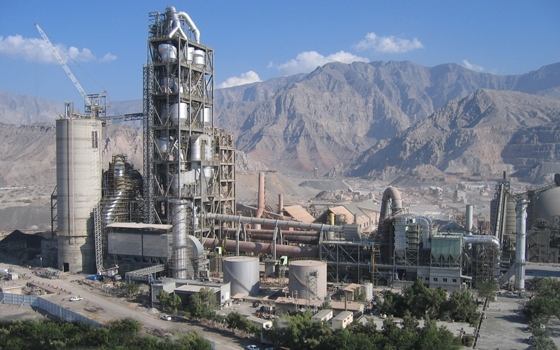
Cement is one of the most important materials in the world, essential for building infrastructure, roads, bridges, and homes. But while many of us see the final product in concrete or mortar, the journey from raw materials to a finished product is intricate and highly technical. This blog will take you through the entire process of how cement is made in modern factories, showcasing the advanced technologies and innovations that drive the industry today.
Introduction
Cement has long been the backbone of the construction industry, providing strength and durability to countless projects. Modern cement factories have evolved to become highly efficient and sustainable, ensuring that the production process is as streamlined and environmentally friendly as possible. In this blog, we’ll explore the complete step-by-step process of cement production, highlighting the key phases and innovations along the way.
1. Raw Material Extraction
The journey of cement production begins with the extraction of raw materials, primarily limestone, which is the cornerstone of cement production. Modern factories rely on efficient quarrying techniques to extract limestone and other materials that are essential for making high-quality cement.
- Limestone Quarrying: The primary raw material for cement is limestone, a sedimentary rock rich in calcium carbonate (CaCO3). Quarrying involves blasting large deposits of limestone and breaking them into manageable pieces for transport.
- Other Materials: In addition to limestone, other materials such as clay, shale, silica sand, and iron ore are also used to provide the necessary chemical composition. These materials are mixed with limestone to create a balanced blend for cement production.
These raw materials are then transported to the cement plant, where they are further processed.
2. Crushing and Pre-Blending
Once the raw materials are extracted, they need to be processed into smaller, uniform pieces to ensure consistency in the final product.
- Crushing: The large rocks of limestone and other raw materials are fed into crushers, which break them down into smaller sizes. This step is crucial as it ensures that the materials are manageable for the subsequent stages of production.
- Pre-Blending: The crushed materials are then stored in pre-blending piles. This is an essential step to ensure uniformity in the raw materials before they enter the grinding phase. Pre-blending helps mix the raw materials in correct proportions to ensure that the final product is consistent in quality.
Modern factories employ advanced machinery to automate the crushing and pre-blending process, ensuring efficiency and precision at every step.
3. Raw Meal Grinding
The crushed and pre-blended materials are then ground into a fine powder, known as raw meal, which is crucial for the chemical reactions that occur later in the kiln.
- Grinding Mills: In this stage, the raw materials are ground into a fine powder using vertical roller mills or ball mills. These machines use high pressure and centrifugal force to grind the materials down to the required fineness.
- Homogenization: After grinding, the raw meal is stored in silos, where it is homogenized to ensure that the mixture is uniform. This step is critical in maintaining consistency in the chemical composition of the final product.
Homogenization also helps improve the efficiency of the kiln process, leading to better energy use and lower emissions.
4. Preheating and Precalcining
Before the raw meal enters the kiln, it must be preheated and partially calcined to prepare it for the high temperatures required to form clinker, the intermediate product in cement production.
- Preheater Tower: In modern factories, the raw meal is passed through a preheater tower, where it is heated to about 800°C by hot gases from the kiln. This reduces the energy required in the kiln, making the process more efficient.
- Precalciner: The preheated raw meal then passes through a precalciner, where it undergoes calcination. During calcination, the calcium carbonate in the limestone decomposes into calcium oxide (CaO) and carbon dioxide (CO2). This is a critical step in the formation of clinker and greatly reduces the energy consumption in the kiln.
This stage is a key innovation in modern cement factories, allowing for lower energy use and reduced carbon emissions.
5. Clinker Production in the Kiln
The kiln is the heart of any cement manufacturing plant, where the raw materials are transformed into clinker through intense heat and chemical reactions.
- Rotary Kiln: The rotary kiln is a large, cylindrical furnace that rotates slowly while being heated to temperatures as high as 1450°C. At these extreme temperatures, the raw materials undergo chemical reactions that form clinker.
- Clinker Formation: Inside the kiln, the raw materials undergo a series of chemical changes, including the formation of compounds such as tricalcium silicate, dicalcium silicate, and tricalcium aluminate. These compounds give clinker its characteristic hardness and strength.
The production of clinker is the most energy-intensive step in the cement manufacturing process, and modern factories use advanced technology to optimize energy use and minimize environmental impact.
6. Clinker Cooling
After the clinker is formed in the kiln, it must be cooled rapidly to preserve its quality and prepare it for grinding.
- Clinker Cooler: Modern cement plants use a clinker cooler to rapidly reduce the temperature of the clinker from 1450°C to around 100°C. This process is crucial for maintaining the chemical properties of the clinker and ensuring that it is ready for the next stage of production.
- Heat Recovery: The heat generated during the cooling process is often recovered and used to preheat the raw meal in the preheater tower, further improving energy efficiency.
The cooled clinker is then ready for the final stages of production, where it will be ground into cement.
7. Cement Grinding
The final step in the production of cement involves grinding the cooled clinker into a fine powder and adding additives to create the desired properties in the finished product.
- Grinding Clinker: The clinker is ground in ball mills or vertical roller mills along with small amounts of gypsum, which is added to control the setting time of the cement. The fineness of the grind is carefully controlled to ensure the proper texture and performance of the cement.
- Additives: Depending on the type of cement being produced, other additives such as fly ash, slag, or limestone may be added to improve performance and sustainability.
The resulting product is a fine powder known as cement, ready for use in construction projects around the world.
8. Packaging and Shipping
Once the cement is produced, it must be packaged and distributed to customers.
- Cement Storage: In modern factories, cement is stored in large silos before being packaged for distribution. The silos ensure that the cement is protected from moisture and contamination.
- Packaging: Cement can be packaged in bags for smaller quantities or shipped in bulk for large projects. Automated packaging systems are used in most modern factories to ensure fast and efficient handling of the product.
The cement is then transported to construction sites via trucks, trains, or ships, ready to be used in a wide variety of applications.
9. Quality Control and Testing
Throughout the entire manufacturing process, quality control plays a critical role in ensuring that the final product meets the required standards for strength, durability, and performance.
- Testing: Modern cement factories have advanced laboratories where raw materials, clinker, and cement are tested for various properties such as chemical composition, fineness, and compressive strength.
- X-ray Fluorescence (XRF) Technology: Many plants use XRF technology to analyze the chemical composition of the raw materials and the final product. This technology allows for precise control over the production process, ensuring consistent quality.
By maintaining rigorous quality control standards, cement manufacturers can produce a reliable and high-performance product that meets the needs of the construction industry.
10. Sustainability in Cement Manufacturing
As the world becomes more focused on sustainability, modern cement factories are adopting new technologies and practices to reduce their environmental impact.
- Energy Efficiency: Modern factories use energy-efficient machinery and processes to reduce the amount of energy required to produce cement. For example, heat recovery systems and the use of alternative fuels can significantly lower energy consumption.
- Alternative Fuels: Many cement plants are now using alternative fuels such as biomass, waste-derived fuels, and even recycled materials to reduce their reliance on fossil fuels and decrease carbon emissions.
- Carbon Capture and Storage (CCS): Some factories are exploring carbon capture and storage technologies to trap and store CO2 emissions from the cement production process, reducing their environmental footprint.
These sustainability efforts are helping cement manufacturers reduce their carbon emissions and make cement production more environmentally friendly.
Conclusion
The process of how cement is made in modern factories involves a combination of advanced technology, precise engineering, and rigorous quality control. From raw material extraction to the final packaging of cement, every step is designed to ensure efficiency, sustainability, and high performance. As the industry continues to evolve, the adoption of innovative techniques and a focus on environmental responsibility will play an increasingly important role in shaping the future of cement production.
Whether you’re a Cement Plant Manufacturing Company or simply curious about the Step By Step Process to Cement Manufacturing, understanding the journey from raw materials to finished cement is essential for appreciating the complexity of this vital industry. Modern factories are constantly refining their processes, ensuring that Everything You Need to Know about cement production is focused on efficiency, quality, and sustainability.
Leave a Reply