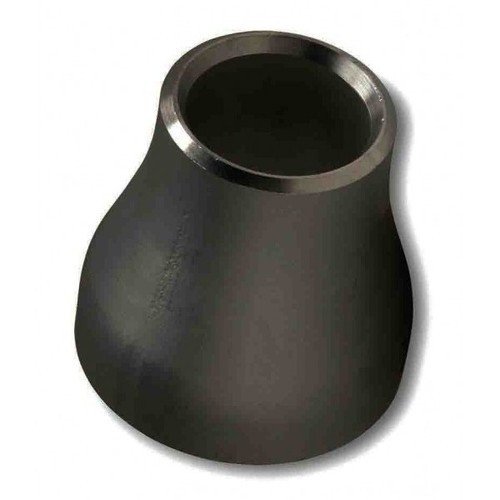
In industrial piping systems, ensuring seamless connections and optimal flow is essential for efficiency and durability. Among the various pipe fittings, Mild Steel Reducers are critical in joining pipes of varying diameters while maintaining smooth flow and structural strength. Due to their affordability, durability, and high performance, these reducers are widely used in industries like oil and gas, petrochemicals, water systems, and construction.
This blog will examine the manufacturing process of high-quality Mild Steel Reducers and highlight their significance in industrial applications.
What are Mild Steel Reducers?
Mild Steel Reducers are pipe fittings that connect two pipes of different diameters. Made from mild steel with a low carbon content, these reducers are known for their strength, flexibility, and ease of fabrication.
Mild steel reducers are available in two main types:
- Concentric Reducers: These connect pipes along the same central axis.
- Eccentric Reducers: Used when pipes need to maintain a consistent level for drainage or flow requirements.
These reducers are vital components in pipelines, ensuring smooth transitions while minimizing turbulence and pressure loss.
Key Steps in the Manufacturing Process of Mild Steel Reducers
Producing mild steel reducers involves precise engineering and quality control to meet industrial standards. Below is an overview of the step-by-step process:
-
Raw Material Selection
The manufacturing process begins with selecting high-quality mild steel. Depending on the reducer type, the raw material typically consists of steel plates or seamless pipes. Mild steel is chosen for its excellent ductility, weldability, and strength, ensuring reliable performance under pressure and temperature variations.
The selected material is inspected for:
- Composition accuracy
- Mechanical properties
- Surface defects
This ensures the quality of the final product.
-
Cutting and Shaping
Once the raw material is approved, it is cut into appropriate sizes based on the required dimensions of the mild steel reducer. Two primary methods are used:
- Hot Forming: The material is heated to a high temperature, making it easier to shape. This method is widely used for larger reducers, as the heat increases the ductility of the mild steel.
- Cold Forming: In this process, the material is shaped at room temperature using high-pressure forming machines. This method is ideal for smaller reducers and ensures a precise finish.
The cutting and shaping step creates the rough outline of the reducer.
-
Press Forming or Extrusion
To achieve the desired reducer shape, the prepared material undergoes press forming or extrusion:
- Press Forming: The material is placed in a mould and subjected to high pressure. A hydraulic press or mechanical press shapes the steel into a reducer. This method ensures uniform thickness and smooth transitions.
- Extrusion: The extrusion process pushes the steel through a die to form the reducer shape. This method is particularly effective for seamless mild steel reducers.
The process ensures accuracy in dimensions and a seamless structure, which is critical for industrial applications.
-
Welding and Joining (for Welded Reducers)
Steel plates are rolled and welded for welded mild steel reducers to form the desired reducer shape. High-quality welding techniques, such as submerged arc welding (SAW) or gas metal arc welding (GMAW), create strong, leak-proof joints.
Weld seams are inspected thoroughly using:
- Non-Destructive Testing (NDT) to identify any flaws or cracks
- X-ray or Ultrasonic Testing for weld integrity
This step ensures the reducer can withstand high pressure and temperatures.
-
Heat Treatment
After shaping and welding, the reducers undergo heat treatment to enhance their mechanical properties. Heat treatment involves processes like:
- Annealing: Reduces internal stress and improves ductility.
- Normalizing: Enhances toughness and grain structure.
Heat treatment ensures the mild steel reducer is strong, durable, and ready for demanding applications.
-
Surface Treatment and Finishing
Surface treatments protect mild steel reducers from corrosion and enhance their appearance. These treatments include:
- Sandblasting: Removes surface impurities and prepares the reducer for coating.
- Galvanization: A zinc coating protects the steel from rust and corrosion.
- Painting or Powder Coating: Adds an extra protective layer for long-term durability.
Once the surface treatment is complete, the reducers are polished and inspected to ensure a smooth, defect-free finish.
-
Quality Testing and Inspection
Before being dispatched, mild steel reducers undergo stringent quality testing to meet industry standards like ASME, ASTM, and ANSI. Common tests include:
- Dimensional Inspection: Ensures the reducers meet specified sizes and tolerances.
- Pressure Testing: Verifies the reducers can handle high-pressure conditions without failure.
- Corrosion Resistance Test: Confirms the durability of the surface treatment.
These tests ensure that only high-quality, defect-free reducers reach the market.
Applications of Mild Steel Reducers
Due to their versatility and strength, mild steel reducers are used in various industries, including:
- Oil and Gas: For seamless pipeline flow transporting crude oil, natural gas, and petroleum products.
- Power Plants: Essential for steam and water systems in thermal, nuclear, and hydroelectric plants.
- Water Distribution: Used in municipal water pipelines and sewage systems.
- Construction: Critical for HVAC systems, plumbing, and structural pipelines.
- Chemical and Petrochemical Industries: For handling high-pressure chemicals and fluids.
Providing seamless transitions while maintaining system integrity makes mild steel reducers indispensable in these sectors.
The detailed and carefully monitored manufacturing process ensures that Mild Steel Reducers deliver unmatched strength, reliability, and performance across industries. Their role in enabling smooth, durable connections in piping systems highlights their importance in modern infrastructure.
Leave a Reply