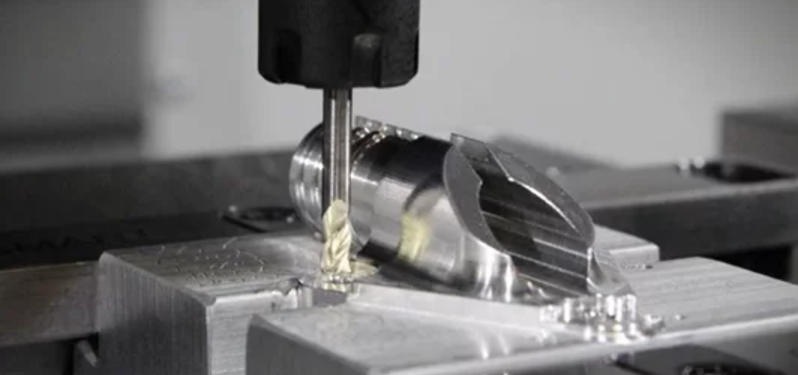
Chatter is a common issue in machining that can have a significant impact on the quality of a finished part, tool life, and overall machining efficiency. It is a type of vibration that occurs during the Chatter in Machining, and it can cause undesirable patterns on the workpiece, reduced tool life, and even machine damage. In this article, we will delve into what chatter is, the causes behind it, the effects it has on machining, and how to prevent or mitigate it to ensure optimal performance in your machining operations.
What is Chatter in Machining?
Chatter in machining refers to the unwanted vibrations that occur between the cutting tool and the workpiece. These vibrations result from an interaction between the machine toolโs natural frequencies, the cutting forces, and the workpiece material. Chatter is a dynamic and unstable phenomenon, and it can cause the cutting tool to intermittently lose contact with the workpiece, followed by a sudden re-engagement, which leads to a repetitive pattern of impacts.
In practical terms, chatter manifests as oscillations or “bouncing” of the cutting tool, which can result in a poor surface finish, excessive tool wear, and inaccurate dimensions. Chatter can occur in any machining operation, whether itโs milling, turning, drilling, or grinding. The problem is most noticeable when the cutting conditions or machine setup are not optimized.
Causes of Chatter in Machining
Chatter is caused by a variety of factors, often working together. It typically occurs when the cutting forces exceed the stability limits of the machine, tool, and workpiece. Below are some common causes of chatter in machining:
1. Resonance and Natural Frequencies
All machine tools, cutting tools, and workpieces have natural frequencies that are characteristic of their design and material properties. When the frequency of the cutting forces aligns with the natural frequency of the system (machine-tool-workpiece), resonance occurs. This amplifies the vibrations and can lead to instability, resulting in chatter. Essentially, the system “sings” at its resonant frequency, causing excessive oscillations.
2. Cutting Force Imbalances
The cutting forces generated during machining, such as radial, axial, and tangential forces, can cause the tool to deflect and vibrate. These forces fluctuate during the cutting process, especially if the tool encounters uneven material properties or inconsistent geometry. If the tool is not rigid enough to withstand these fluctuating forces, it will vibrate, resulting in chatter.
Additionally, cutting forces are affected by factors such as tool geometry, material hardness, and cutting parameters (speed, feed rate, and depth of cut). Excessive cutting forces or poor distribution of these forces can lead to vibrations and chatter.
3. Tool Geometry and Condition
The condition and geometry of the cutting tool play a crucial role in preventing chatter. If the tool has worn edges, irregular cutting faces, or improper geometry (e.g., incorrect rake angles), it will not cut smoothly. This causes uneven cutting forces, which in turn leads to vibrations and chatter. Sharp, well-maintained tools with optimized geometry help reduce these oscillations and ensure smooth cutting.
4. Machine Rigidity
The overall rigidity of the machine tool and its components is a key factor in preventing chatter. If the machineโs structure is weak, or if there is excessive play or deflection in the spindle, tool holder, or workpiece, the cutting tool may move unpredictably during the cutting process. This lack of rigidity can lead to vibration, resulting in chatter. Proper machine alignment, stability, and minimizing tool overhangs can reduce the likelihood of chatter.
5. Cutting Speed and Feed Rate
Both the cutting speed and feed rate have a direct impact on chatter. High cutting speeds can increase the likelihood of resonance, especially if the speed is too high for the material being cut. Similarly, an excessively high feed rate may lead to more aggressive cutting forces, further exacerbating the vibrations. On the other hand, too low of a feed rate can cause the cutting tool to rub against the workpiece, which can also introduce vibrations.
6. Tool Overhang
The longer the tool overhang (the length of the tool from the holder to the cutting edge), the more likely the tool is to vibrate. Longer tool overhangs reduce the rigidity of the tool, making it susceptible to deflection and chatter. Using shorter tools or reducing tool overhang can help minimize the risk of chatter.
7. Workpiece Material Properties
The material being machined plays a significant role in the occurrence of chatter. Materials with varying hardness, inconsistent grain structure, or uneven surface finishes can cause irregular cutting forces, which may trigger vibrations and lead to chatter. For example, hard materials may cause the cutting tool to “bounce” off the workpiece, resulting in vibrations.
Effects of Chatter in Machining
Chatter is more than just an inconvenience; it has several detrimental effects on machining operations. Below are the main consequences of chatter:
1. Poor Surface Finish
One of the most noticeable effects of chatter is a poor surface finish. The vibrations caused by chatter create a rough, uneven surface on the workpiece. These undulations or “waves” can be seen as visible marks on the part and are undesirable in applications that require a smooth, polished finish. This can lead to additional finishing operations or even part rejection.
2. Increased Tool Wear
Chatter increases the wear and tear on cutting tools. The vibrations caused by chatter create irregular contact between the cutting tool and the workpiece, causing stress and impact on the tool edges. This accelerates tool wear, shortening its lifespan and leading to the need for more frequent tool replacements. In addition to higher costs, tool wear can further worsen the machining process and increase the risk of poor-quality parts.
3. Reduced Dimensional Accuracy
Chatter can cause a lack of control over the cutting process, leading to dimensional inaccuracies. The toolโs vibrations cause it to deviate from its intended cutting path, resulting in parts that do not meet the required tolerances. This is especially problematic in precision machining, where even small deviations can render a part unusable.
4. Increased Cutting Time
To mitigate the effects of chatter, machinists may need to reduce cutting parameters such as speed, feed rate, or depth of cut. While this can help stabilize the process, it typically results in longer cutting times. As a result, productivity is reduced, and more time is spent on each part, leading to increased operational costs.
5. Damage to the Machine Tool
Prolonged chatter can cause serious damage to the machine tool itself. The excessive vibrations can affect the machineโs bearings, spindle, and other components. Over time, this can lead to significant wear or even failure of machine parts, resulting in costly repairs and downtime.
How to Prevent and Mitigate Chatter in Machining
While chatter can be difficult to eliminate entirely, several strategies can help reduce its occurrence and minimize its impact. Here are some effective solutions to prevent and mitigate chatter:
1. Optimize Cutting Parameters
The most straightforward way to prevent chatter is to optimize the cutting parameters. This includes adjusting the cutting speed, feed rate, and depth of cut to find the optimal combination for the material and tool. Slower speeds and lower feed rates often help reduce cutting forces and prevent excessive vibrations.
2. Increase Tool Rigidity
Using shorter tools, proper tool holders, and reducing tool overhang can increase the rigidity of the cutting system and reduce the risk of chatter. Rigidity helps prevent the tool from deflecting and maintains stable cutting forces, making the machining process more controlled and predictable.
3. Stabilize the Machine Setup
A stable and well-secured workpiece is essential to prevent chatter. Ensure that the workpiece is clamped tightly to the machine bed and that the tool is properly aligned with the part. Minimizing any potential movement during cutting will reduce the chances of vibration.
4. Use Damping Systems
Many modern CNC machines are equipped with vibration-damping systems designed to absorb and reduce unwanted oscillations. These systems can help stabilize the cutting process and prevent chatter from escalating.
5. Select the Right Tool Geometry and Material
Choosing the right cutting tool geometry and material for the job can help reduce chatter. Tools with sharp cutting edges and appropriate coatings can reduce cutting forces and improve the overall machining process. Additionally, using tools made from materials with higher rigidity can minimize vibrations.
6. Machine Maintenance
Regular maintenance of both the cutting tool and the machine tool is essential for preventing chatter. Worn tools should be replaced or re-sharpened, and the machine should be regularly calibrated to ensure it is operating within the desired tolerances.
7. Use a Slower Approach
When chatter occurs, reducing the depth of cut or using a lighter approach can help mitigate the effects. Taking smaller, more controlled cuts allows for better precision and reduces the likelihood of excessive vibrations.
Conclusion
Chatter in machining is an unavoidable but manageable phenomenon that can significantly impact the quality of your parts, tool life, and machining efficiency. Understanding its causesโsuch as resonance, cutting force imbalances, and tool rigidityโcan help in implementing effective strategies to prevent it. By optimizing cutting parameters, improving tool rigidity, and maintaining machine tools, you can mitigate the effects of chatter and achieve high-quality, accurate parts with minimal downtime and tool wear. With proper planning, monitoring, and maintenance, machinists can reduce chatter and enhance the overall performance of their machining operations.
Leave a Reply