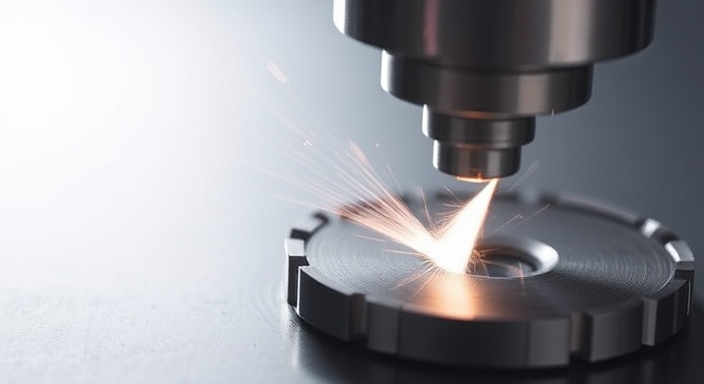
In the world of manufacturing, where precision and efficiency are critical, the tools used often determine the success of a project. While standard cutting tools work well for general applications, specialized or complex manufacturing requirements require something better and more accomplished.
Custom cutting tools provide tailored solutions designed specifically for unique production challenges. They improve precision, efficiency, and cost-effectiveness, and have been revolutionizing specialized manufacturing processes. Read on to learn more about these tools, their use in different sectors, and their benefits.
What Are Custom Cutting Tools?
Custom cutting tools meet the specific needs of a manufacturing process. Unlike standard tools, produced in bulk for a wide range of applications, custom tools focus on the exact requirements of a particular task. These tools can be designed to handle specific materials, accommodate unique geometries, or streamline complex processes. Their bespoke nature makes them an essential asset in industries like aerospace, automotive, medical device manufacturing, and energy production, where precision and reliability are paramount.
Benefits of Custom Cutting Tools
One of the key advantages of custom cutting tools is their ability to deliver unmatched precision. Since they help accomplish specific tasks, inconsistencies often associated with using standard tools for specialized applications get eliminated. This level of accuracy ensures high-quality results, even for intricate designs or tight tolerances. Efficiency is another notable benefit. These tools can be optimized for the specific machining conditions of a project, reducing cycle times and improving productivity.
In many cases, they can combine multiple functions into a single tool, streamlining the manufacturing process and minimizing tool changes. Cost savings, while not immediately apparent due to the upfront investment, are significant in the long term. Custom tools reduce material waste, minimize rework, and eliminate the need for multiple standard tools, all of which contribute to lower overall production costs. Custom cutting tools also excel in handling challenging materials. Whether itβs composites, hardened steels, or exotic alloys, these tools help meet the demands of even the most difficult-to-machine materials, extending tool life and improving overall performance.
Applications of Custom Cutting Tools
Custom cutting tools find applications in various industries where precision and performance are critical. In aerospace, they are used to machine lightweight, durable materials for aircraft components. Automotive manufacturers rely on them to produce complex engine parts with exacting standards. In the medical field, they play a crucial role in crafting intricate surgical instruments and implants. The energy sector also benefits from its ability to handle the demanding requirements of components for wind turbines, oil rigs, and other systems. These applications highlight the versatility of custom cutting tools in addressing industry-specific challenges and achieving superior results.
Why Choose Custom Cutting Tools?
Opting for custom cutting tools often arises when standard tools struggle to meet specific production needs. For instance, if a project involves manufacturing parts with unique geometries, intricate designs, or tight tolerances, custom tools are ideal. They also shine in high-volume production runs, where efficiency and durability are critical.Β
Additionally, when working with materials that are difficult to machine, custom tools ensure the process is effective and efficient. By designing the tool to handle the materialβs properties, manufacturers reduce tool wear and improve cutting performance.
Partnering with the Right Toolmaker
To fully benefit from custom cutting tools, it is important to collaborate with an experienced tool manufacturer. A skilled toolmaker will assess the specific requirements of your project, including material type, dimensions, and production volume, to design a tool that meets your needs. Clear communication during the design and prototyping phases ensures the final tool delivers optimal performance and longevity.
Conclusion
Custom cutting tools are transforming the manufacturing landscape by addressing the limitations of standard tools. Their ability to enhance precision, improve efficiency, and reduce costs makes them an invaluable resource for specialized applications. While the initial investment in custom tools may be higher, the long-term benefits in quality, productivity, and cost savings far outweigh the expense. For manufacturers dealing with complex designs, challenging materials, or high-volume production, custom cutting tools offer a strategic advantage, helping execute every project with excellence.
Leave a Reply